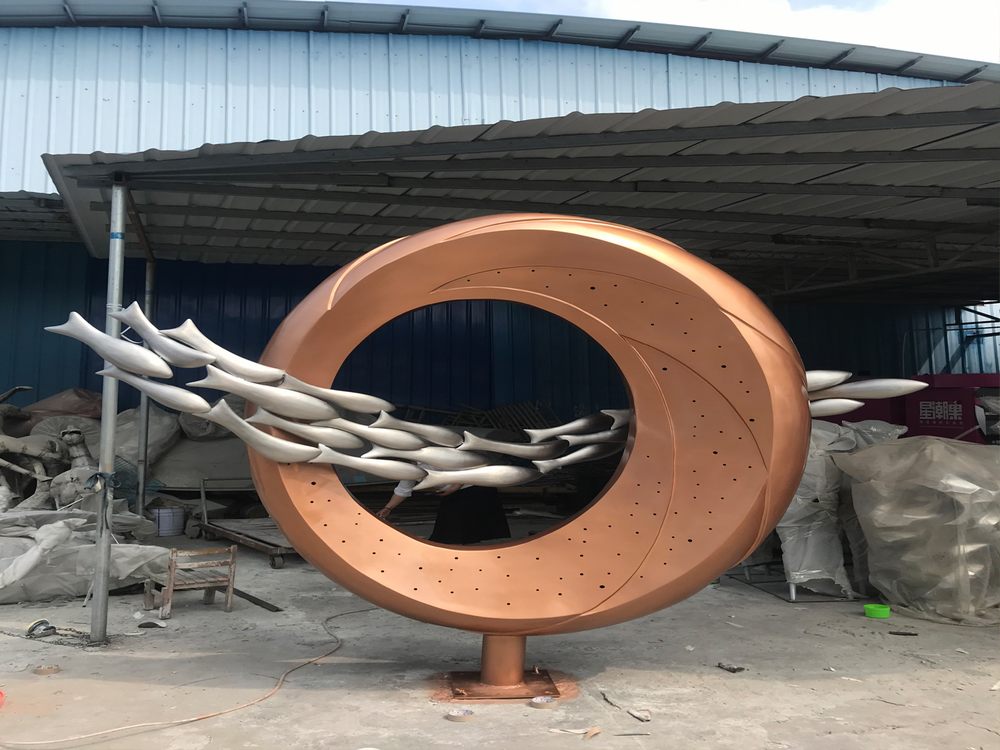
Creating durable and visually appealing pottery requires meticulous attention to the drying and firing stages, where cracking and warping are common challenges. Artisans employ a combination of time-tested techniques and modern innovations to ensure their ceramic pieces remain intact.
1. Controlled Drying Process:
- Slow, even drying is critical. Artisans often cover pieces with plastic or damp cloths to regulate moisture loss, preventing uneven shrinkage that leads to cracks.
- Thicker pieces are dried upside down to balance evaporation rates.
2. Proper Clay Preparation:
- Wedging clay thoroughly removes air bubbles, which can expand during firing and cause cracks.
- Using the right clay body (e.g., grogged clay for larger pieces) enhances structural stability.
3. Kiln Firing Strategies:
- A gradual temperature increase during bisque firing allows residual moisture to escape safely.
- Cone packs or digital controllers ensure precise temperature management, reducing thermal shock risks.
4. Supportive Techniques:
- Kiln shelves are coated with batt wash to prevent glaze adhesion and warping.
- Warp-prone items like plates are fired on stilts or sand beds to maintain shape.
By mastering these methods, artisans transform fragile clay into resilient, beautiful ceramics, preserving both form and function.