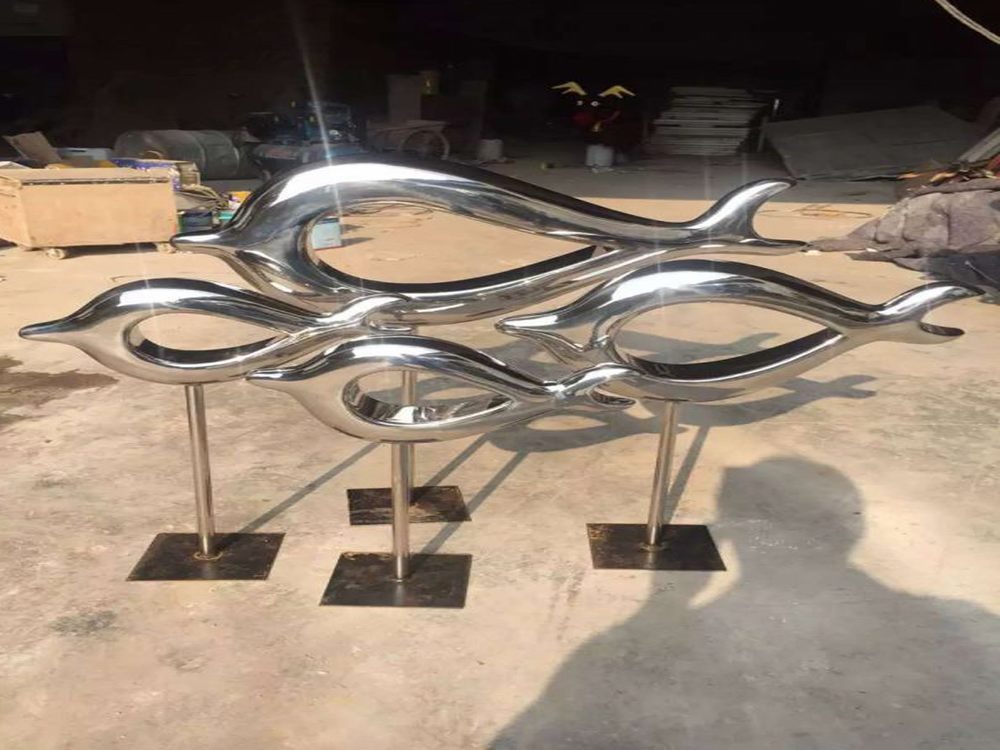
Creating handmade porcelain sculptures is a delicate art form that demands precision, patience, and unparalleled craftsmanship. However, maintaining consistent quality across each piece presents several challenges.
1. Material Variability: Porcelain clay can differ in composition and behavior, even within the same batch. Slight variations in moisture content or mineral impurities can affect the final product’s strength and appearance.
2. Artisan Skill and Fatigue: Each sculpture relies heavily on the artisan’s expertise. Fatigue or minor inconsistencies in technique can lead to uneven shapes, flawed details, or cracks during drying and firing.
3. Firing Process Uncertainties: Kiln temperature fluctuations or uneven heating may cause warping, discoloration, or breakage. Achieving the perfect glaze finish also requires precise timing and conditions.
4. Time-Intensive Nature: Handmade pieces require meticulous attention at every stage, from shaping to painting. Rushing any step can compromise quality, making scalability difficult without sacrificing standards.
5. Repair and Finishing Challenges: Unlike mass-produced items, flaws in handmade sculptures often require painstaking repairs or complete restarts, adding to production time and costs.
Despite these challenges, the uniqueness and artistry of handmade porcelain sculptures remain unmatched. Master artisans mitigate these issues through years of experience, rigorous quality checks, and a deep understanding of their materials. For collectors, these subtle imperfections often enhance the piece’s charm, celebrating the human touch behind each creation.