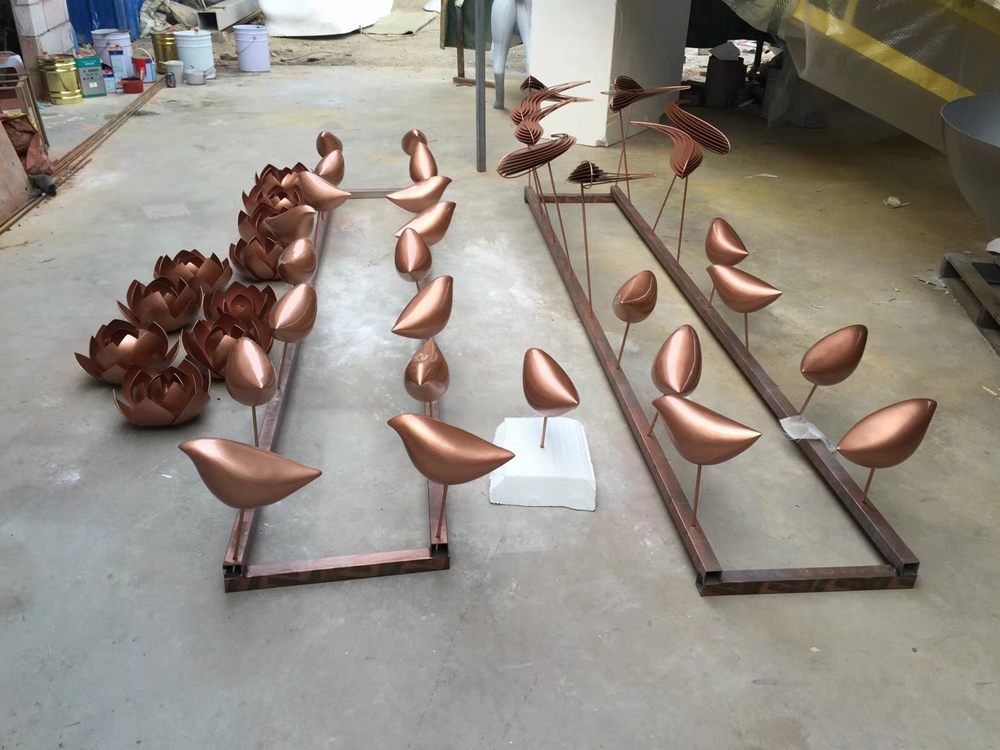
Porcelain sculptures, traditionally associated with delicate indoor displays, have increasingly adapted to the rigors of outdoor public art installations through innovative techniques and material advancements.
1. Enhanced Durability: Modern porcelain formulations incorporate additives like alumina or silica to improve structural integrity, enabling sculptures to withstand environmental stressors such as wind, rain, and temperature fluctuations.
2. Glazing Innovations: Specialized glazes act as protective barriers, resisting UV degradation, moisture penetration, and pollution. High-fired vitreous glazes create non-porous surfaces that prevent cracking in freeze-thaw cycles.
3. Modular Design: Large-scale installations often use segmented porcelain components with reinforced steel armatures, allowing for expansion/contraction while maintaining aesthetic cohesion.
4. Site-Specific Engineering: Artists collaborate with material scientists to tailor sculptures for local climates—thicker walls for colder regions or breathable designs for humid environments.
5. Maintenance Integration: Designs now incorporate self-cleaning nano-coatings or strategic angles to minimize dirt accumulation, reducing long-term upkeep costs for municipalities.
These adaptations transform porcelain from a fragile medium into a viable option for enduring public art, merging artistic expression with engineered resilience.