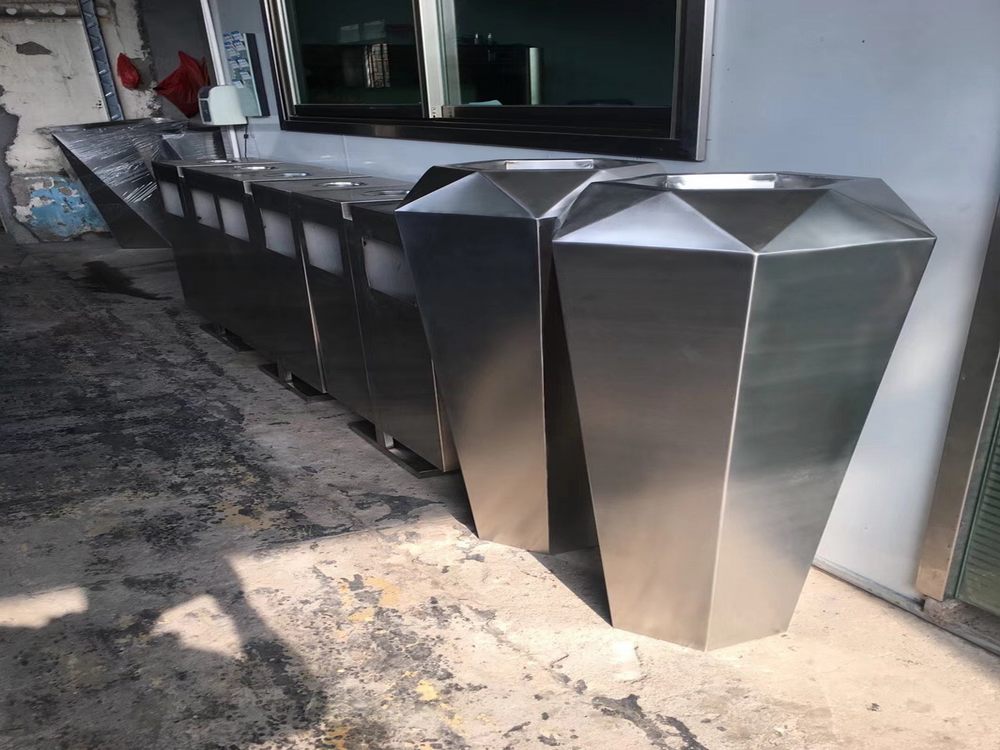
Achieving matte or glossy finishes in porcelain sculpture glazing is a delicate balance of chemistry, technique, and firing precision. For a glossy finish, artists typically use glazes rich in fluxes like silica and feldspar, which melt smoothly during kiln firing to create a reflective, glass-like surface. The higher the silica content and the longer the firing duration, the more pronounced the gloss becomes.
Matte finishes, conversely, result from glazes with higher concentrations of materials like calcium, magnesium, or alumina, which crystallize during cooling, scattering light and creating a soft, non-reflective surface. Some artists also achieve matte effects by under-firing glazes or applying specialized matte coatings post-firing.
The firing temperature plays a crucial role—glossy glazes often require higher temperatures (around 1200-1300°C) to fully vitrify, while matte glazes may be fired at slightly lower temperatures to preserve their texture. Additionally, application methods matter: dipping creates uniform finishes, while brushing or spraying allows for intentional variations between matte and glossy areas.
Modern ceramicists sometimes combine both finishes on a single piece, using wax resist or masking techniques to create striking contrasts. Whether opting for the velvety elegance of matte or the luminous depth of gloss, mastering these effects requires experimentation with glaze formulas, application thickness, and kiln schedules—a testament to the artistry behind porcelain sculpture.