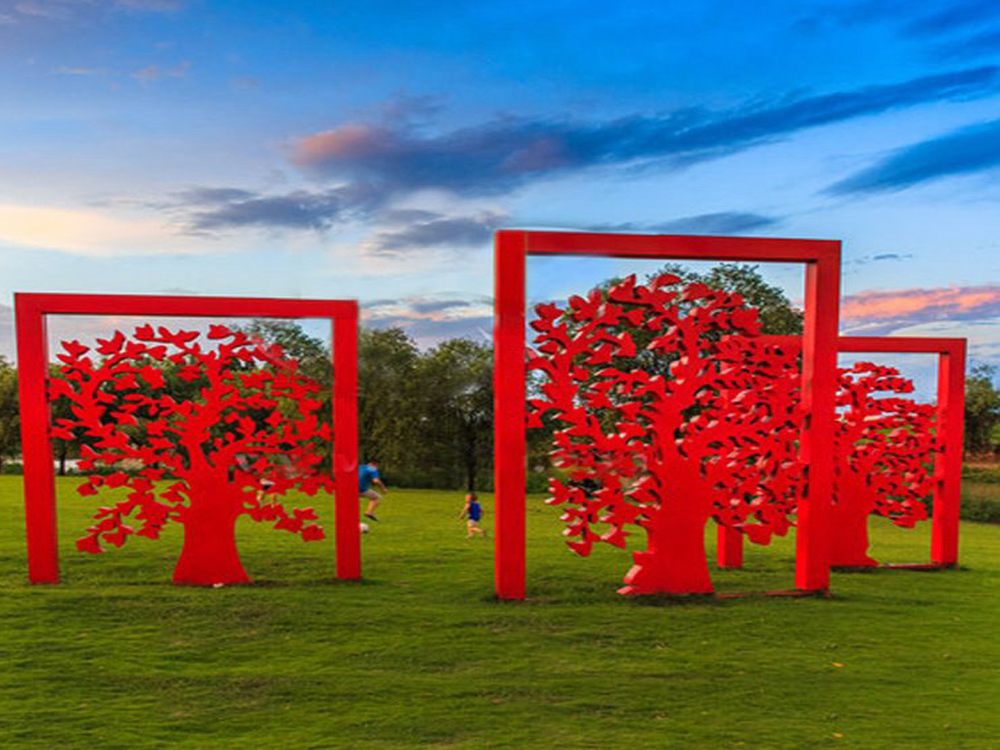
Creating porcelain sculptures with intricate details is a meticulous art form that demands exceptional skill and patience. Artists face the challenge of replicating these delicate features across multiple editions while maintaining consistency and precision. To achieve this, they employ a combination of traditional techniques and modern innovations.
One common method is the use of high-quality molds crafted from the original sculpture. These molds capture every minute detail, allowing artists to produce identical copies. However, even with perfect molds, the fragility of porcelain requires careful handling during casting and firing. Artists often refine each piece by hand, using fine tools to sharpen edges and enhance textures lost in the molding process.
Another technique involves layering thin applications of porcelain slip to build up complex patterns or relief work. This approach ensures depth and dimensionality, critical for lifelike replicas. Additionally, some artists employ digital tools like 3D scanning to create precise models before transitioning to physical production.
Firing presents another hurdle, as porcelain shrinks and can warp. Artists compensate by calculating shrinkage rates and adjusting designs accordingly. Glazing, too, requires expertise—multiple layers may be applied to highlight details, with each firing carefully monitored to avoid flaws.
Ultimately, the success of porcelain sculpture editions lies in the artist’s ability to blend craftsmanship with problem-solving. Through patience, innovation, and an unwavering eye for detail, they transform fragile clay into enduring works of art.