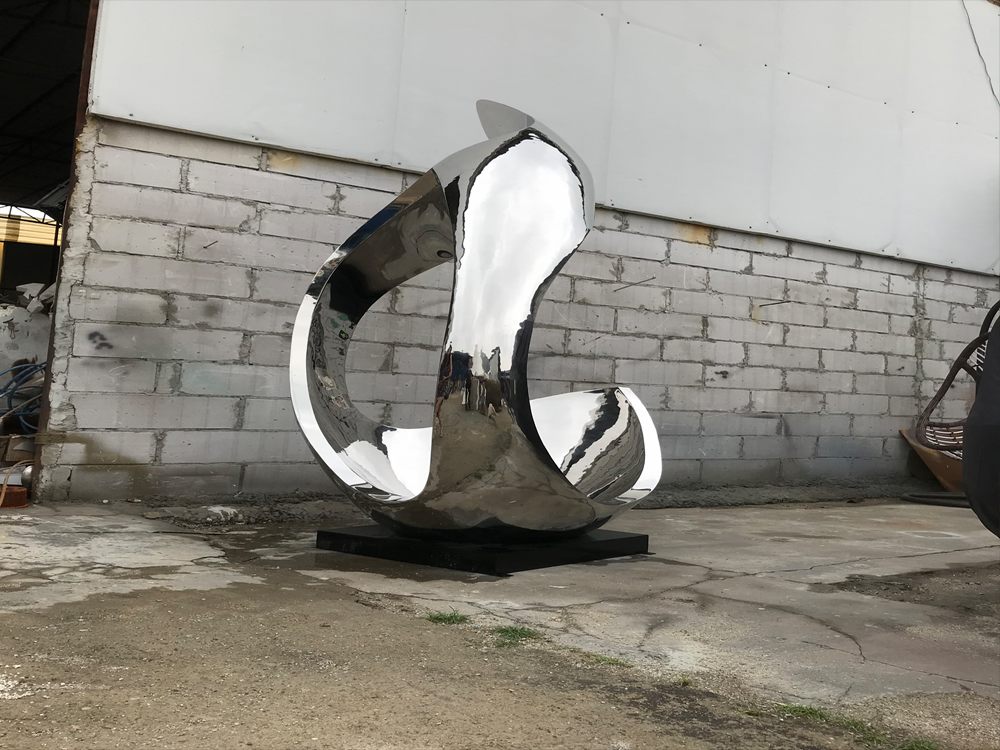
When comparing hand-built and slip-cast porcelain sculptures, several key differences in quality emerge that significantly impact their artistic and functional value. Hand-built porcelain sculptures, crafted entirely by hand using techniques like coiling or slab construction, offer unique organic textures and irregular charm that reflect the artist's personal touch. Each piece carries subtle variations that make it truly one-of-a-kind.
Slip-cast porcelain, created by pouring liquid clay into molds, produces more uniform and precise results with consistent wall thickness. While this method allows for perfect replication of designs, it often lacks the distinctive character of hand-built pieces. In terms of durability, hand-built sculptures typically have thicker walls and stronger structural integrity due to the manual compression of clay particles during creation.
The finishing quality also differs substantially. Hand-built pieces often showcase visible tool marks and intentional imperfections that add artistic value, while slip-cast works tend to have smoother surfaces with factory-like precision. Collectors frequently value hand-built porcelain higher for its craftsmanship and artistic merit, though slip-casting remains popular for mass production and intricate designs difficult to achieve manually.
Ultimately, the choice between these techniques depends on whether one prioritizes artistic uniqueness (hand-built) or technical perfection (slip-cast), with both methods offering distinct advantages in different applications.