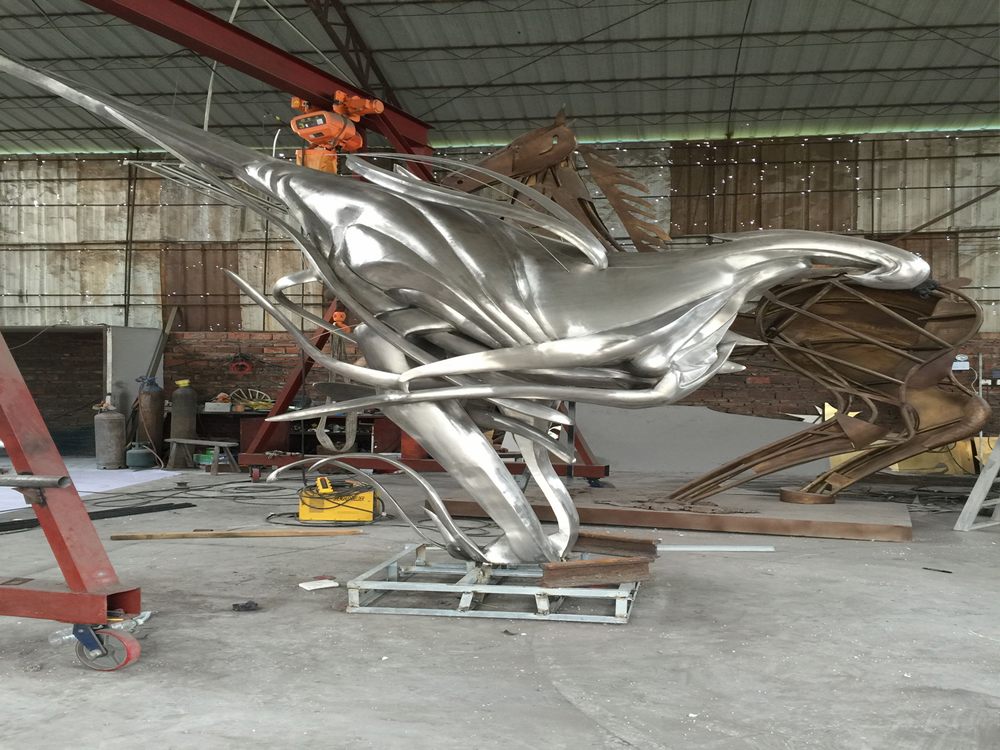
Creating porcelain sculptures with light-reflective or iridescent finishes is a meticulous process that blends artistry with scientific precision. Artists begin by selecting high-quality porcelain clay, known for its smooth texture and ability to hold intricate details. The magic lies in the glazes and firing techniques.
For light-reflective finishes, artists often use metallic glazes containing minerals like titanium or zinc oxide, which create a mirror-like sheen when fired at high temperatures. Iridescent effects, on the other hand, are achieved through specialized glazes infused with metal oxides (e.g., cobalt or copper) or by applying thin layers of lustre after the initial firing. These layers refract light, producing a rainbow-like shimmer.
The kiln plays a crucial role. Controlled firing schedules—sometimes involving multiple firings at varying temperatures—ensure the glazes bond perfectly with the porcelain. Reduction firing (limiting oxygen) can enhance metallic effects, while oxidation firing (adding oxygen) brightens colors.
Innovative techniques like nano-coatings or embedding glass particles are also gaining popularity, pushing the boundaries of porcelain art. Each piece becomes a testament to the artist’s skill in harmonizing chemistry, heat, and creativity.