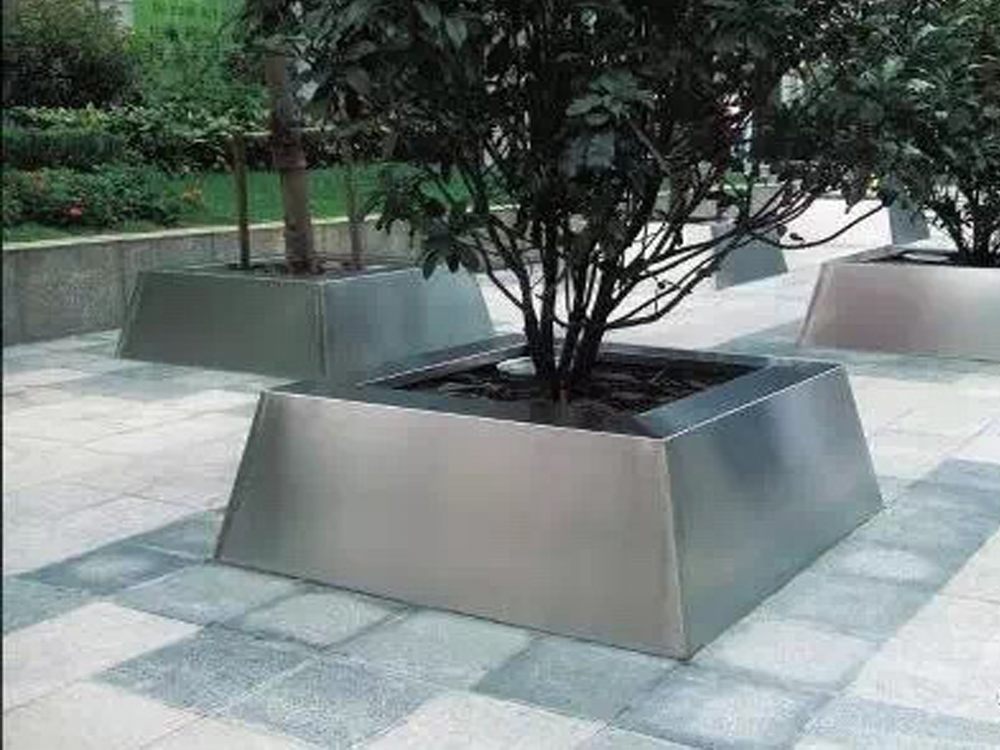
Artists working with porcelain sculptures often face the challenge of firing pieces of varying sizes, from delicate miniatures to large-scale installations. Modular kiln setups provide a versatile solution, allowing creators to customize their firing environment for optimal results.
The key advantage of modular kilns lies in their adjustable components. Artists can rearrange insulating bricks, heating elements, and shelves to create compartments tailored to each sculpture's dimensions. For smaller pieces, compact sections ensure efficient heat distribution, while larger works benefit from expanded chambers with reinforced structural support.
Temperature control is another critical factor. Modular systems enable artists to create zones with different heat levels, accommodating thicker sections that require slower firing or intricate details needing precise thermal management. Advanced setups may include multiple thermocouples to monitor variations across the kiln's interior.
Many ceramicists employ a "nesting" technique, where sculptures are positioned with calculated spacing to promote even airflow. Some kilns feature removable partitions, allowing artists to fire several medium-sized pieces simultaneously or combine sections for a single large work.
The modular approach also supports experimental techniques. Artists might configure one area for rapid bisque firing while maintaining a slower cooling zone elsewhere. This flexibility has revolutionized contemporary porcelain art, enabling more ambitious projects and reducing the risks of thermal shock or uneven curing.
By mastering modular kiln configurations, artists expand their creative possibilities while maintaining technical precision - an essential balance in the delicate art of porcelain sculpture.