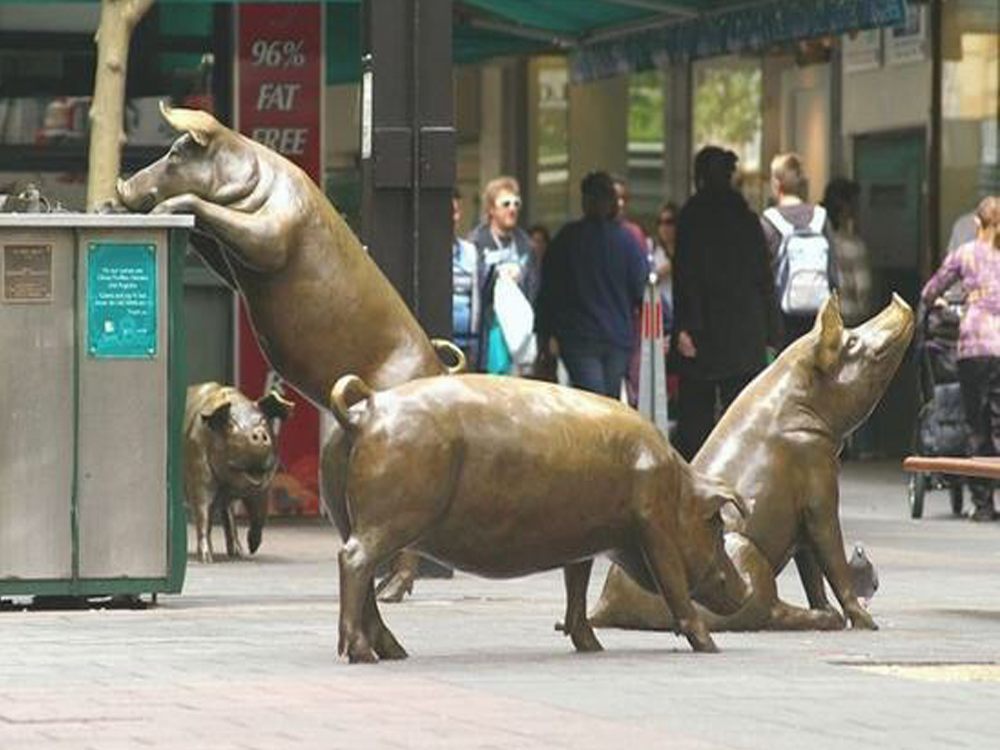
Achieving uniform glaze thickness across intricate porcelain sculpture surfaces is a persistent challenge for ceramic artists. The complexity arises from several factors, including the sculpture's geometry, glaze viscosity, and application methods.
One primary obstacle is the varying absorption rates of different clay body areas. Thinner sections dry faster, absorbing glaze unevenly compared to thicker parts. Additionally, intricate details like undercuts or fine textures trap excess glaze while flat areas may appear under-coated.
The glaze's rheological properties play a crucial role. Overly thick mixtures create pooling in recesses, while thin glazes run off vertical surfaces. Temperature fluctuations during application further complicate consistency, as glaze viscosity changes with environmental conditions.
Application technique significantly impacts results. Dipping often creates uneven coverage on complex forms, while spraying requires meticulous control to avoid thin spots. Brush application demands exceptional skill to maintain uniformity across varied surfaces.
Firing presents additional challenges. Glaze movement during heating can redistribute unevenly, especially on sculptural pieces with multiple angles. Thermal expansion differences between clay and glaze may cause cracking or peeling in areas with inconsistent thickness.
Experienced artists employ various solutions: custom glaze formulations adjusted for specific forms, multiple thin applications, or targeted spraying techniques. Some pre-treat surfaces with resist materials to control absorption, while others rotate pieces during application for better coverage. Understanding these challenges is fundamental to mastering the art of porcelain glazing.