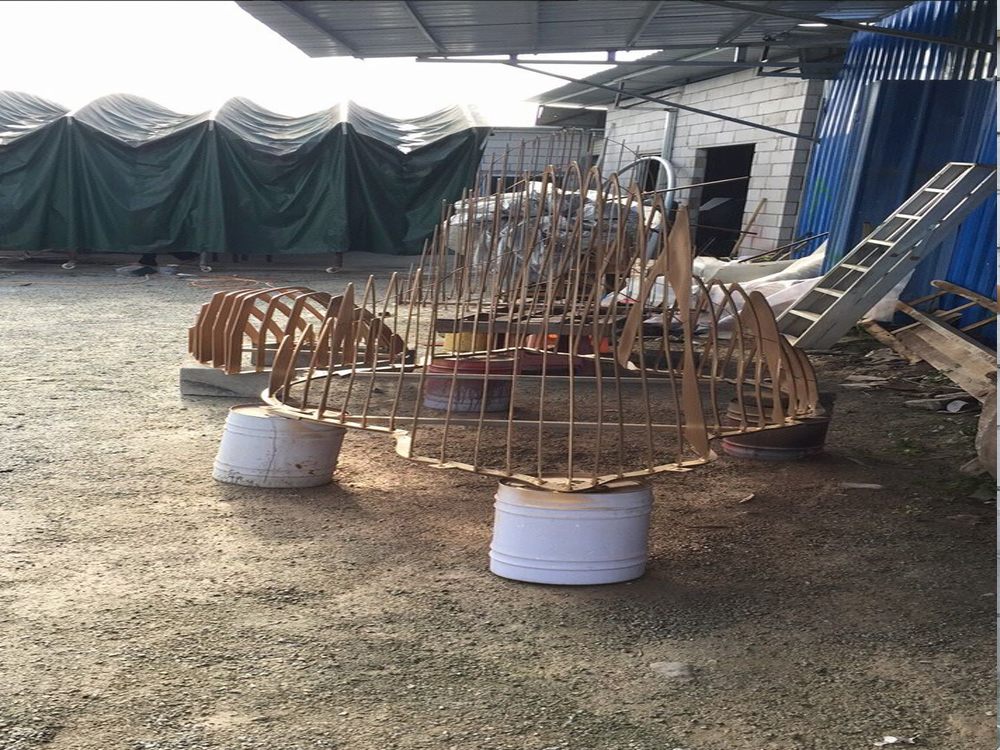
Creating porcelain sculptures with moving parts is a delicate art form that demands both technical precision and artistic vision. Artists face unique challenges in balancing the fragility of porcelain with the functionality of movable components.
One key technique involves carefully designing joints and hinges to minimize stress on the porcelain. Many artists use metal or reinforced ceramic elements at connection points, ensuring durability without compromising aesthetics. The drying and firing processes require special attention, as different parts may shrink at varying rates.
Innovative approaches include creating interlocking pieces that move smoothly after firing, or designing sculptures where movement occurs through natural forces like air currents. Some artists employ slip-casting methods to produce identical components that fit together precisely, while others hand-build each piece for organic movement.
Temperature control during firing is critical, as porcelain can warp or crack if heated unevenly. Artists often fire moving parts separately at slightly different temperatures before final assembly. The glazing process presents another challenge, requiring formulas that won't inhibit movement after firing.
Contemporary artists are pushing boundaries with porcelain kinetics, incorporating modern engineering principles while maintaining traditional ceramic craftsmanship. These creations demonstrate how centuries-old materials can achieve dynamic, interactive art forms through innovative problem-solving and technical mastery.