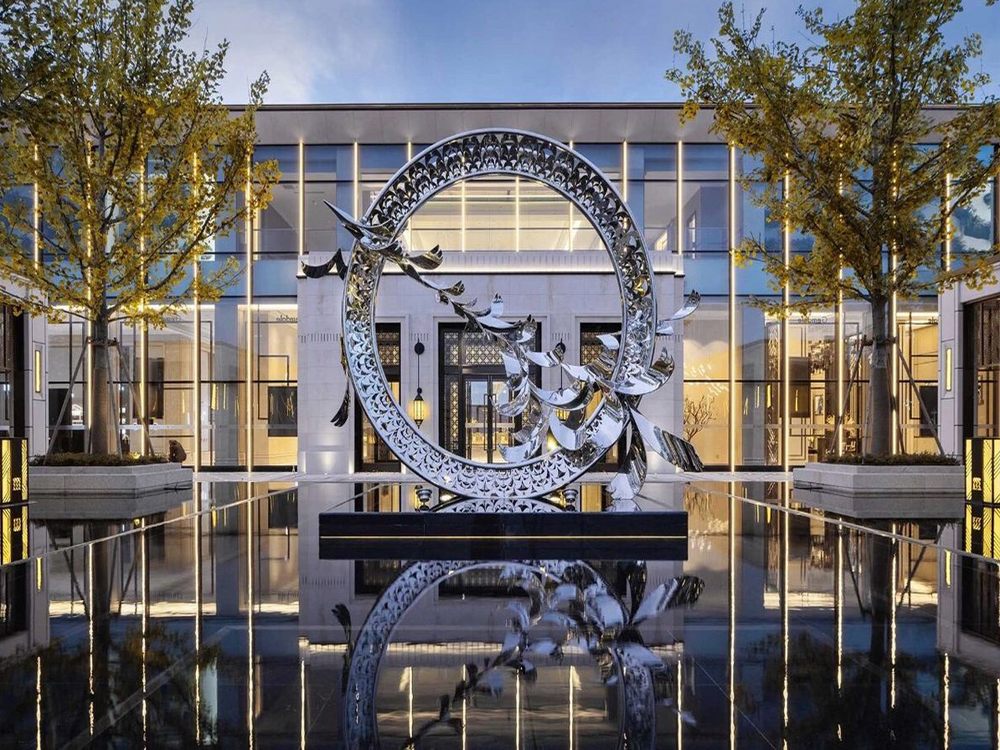
The marriage of ancient ceramic artistry with modern 3D printing technology has birthed extraordinary innovations in porcelain sculpture. Leading this revolution is the creation of impossible geometries – intricate lattice structures and interlocking forms that defy traditional hand-building techniques. Artists now employ gypsum-based binder jetting to produce delicate, hollow-core sculptures with internal channels that would collapse using conventional methods.
Biomorphic designs represent another frontier, where 3D scanning captures organic patterns from nature which are algorithmically enhanced before printing in porcelain clay. This allows for perfect replication of complex biological structures like coral formations or microscopic organisms at varying scales.
Customizable porcelain wearables have emerged through selective laser sintering (SLS) of fine ceramic powders, enabling jewelry designers to create lightweight, durable pieces with personalized textures. Meanwhile, architectural ceramicists are printing large-scale porcelain tiles with embedded functional elements – from acoustic dampening cavities to hidden structural reinforcements.
Perhaps most groundbreaking is 4D printed porcelain, where programmed material transformations occur post-printing. These "smart" sculptures change shape when exposed to moisture or temperature shifts, creating dynamic artworks that evolve over time. As 3D printing materials advance, we're witnessing the rebirth of porcelain – no longer constrained by the limitations of the potter's wheel but liberated by digital craftsmanship.