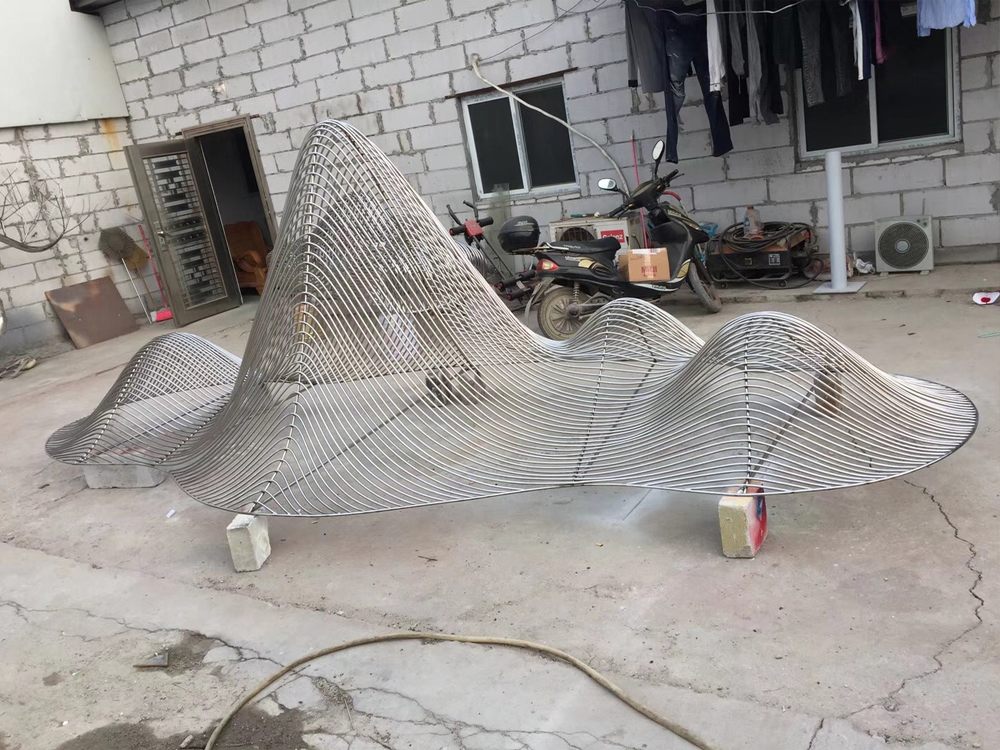
Public art installations featuring porcelain sculptures face unique challenges when exposed to outdoor elements, yet innovative techniques ensure their longevity. High-quality porcelain, fired at extreme temperatures (often exceeding 1,300°C), develops a vitrified surface that resists moisture penetration—a critical factor preventing frost damage in cold climates.
Modern installations incorporate three key protective measures:
1. Specialized glaze formulations with UV inhibitors prevent color fading from sunlight exposure
2. Structural designs incorporating drainage systems to avoid water pooling
3. Microcrystalline wax coatings that create hydrophobic barriers without altering visual appearance
Engineers often place sculptures on elevated stainless steel bases to prevent ground moisture absorption, while periodic maintenance (typically every 3-5 years) involves reapplying protective sealants. Some artists now blend porcelain with polymer composites, creating hybrid materials that maintain ceramic aesthetics while achieving 300% greater impact resistance.
Notable examples like Shanghai's "Porcelain Wave" installation demonstrate how proper engineering allows delicate-looking porcelain to withstand typhoon-force winds through internal titanium reinforcement frameworks. These solutions transform porcelain from fragile tableware material into durable public art medium capable of surviving decades outdoors.