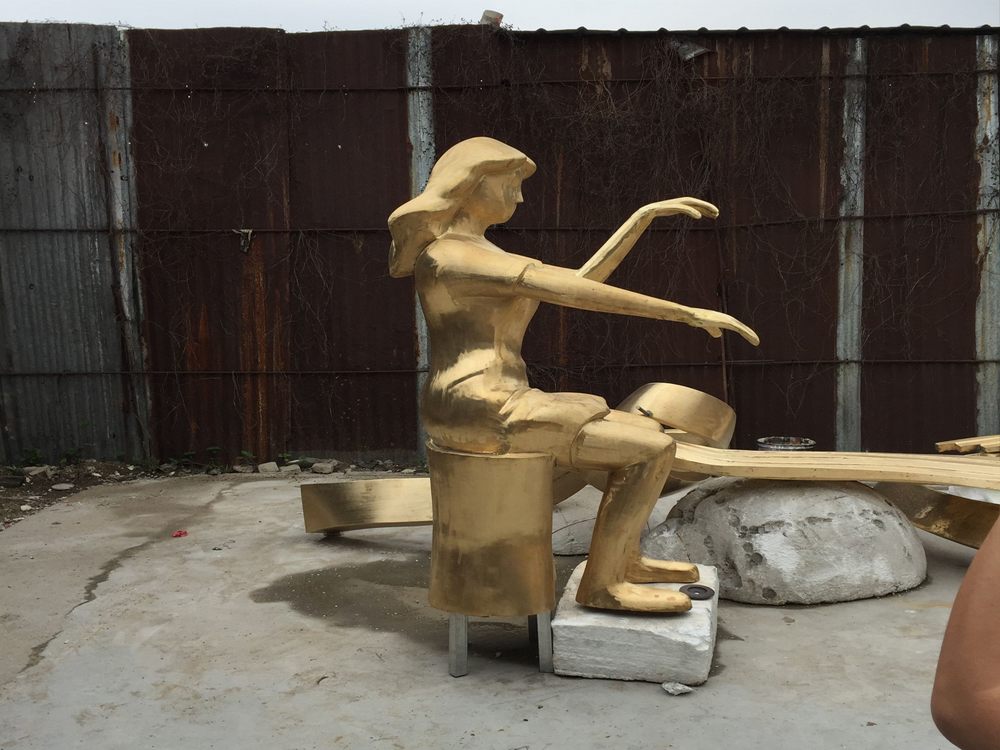
Creating a porcelain sculpture is a meticulous and labor-intensive process that demands precision, patience, and artistic skill. The journey from raw materials to a finished masterpiece involves several critical stages, each requiring significant effort and expertise.
1. Clay Preparation: The foundation of any porcelain sculpture begins with preparing the clay. This stage involves wedging and kneading the clay to remove air bubbles and achieve a uniform consistency. Any imperfections at this stage can lead to cracks or breaks during firing.
2. Hand Sculpting: Unlike mass-produced items, porcelain sculptures are often shaped by hand. Artists spend hours meticulously carving, smoothing, and detailing the clay to bring their vision to life. This stage is particularly labor-intensive due to the delicate nature of porcelain and the need for precision.
3. Drying: After sculpting, the piece must dry slowly and evenly to prevent warping or cracking. This process can take days or even weeks, depending on the size and complexity of the sculpture.
4. Kiln Firing: Porcelain sculptures are fired at extremely high temperatures (often above 1,200°C) to achieve their signature strength and translucency. The firing process is risky, as temperature fluctuations can cause the piece to break or deform.
5. Glazing and Refiring: If the sculpture requires color or a glossy finish, glazing is applied before a second firing. This stage adds another layer of complexity, as the glaze must be applied evenly and fired at precise temperatures.
Each of these stages requires careful attention and skilled hands, making porcelain sculpture creation a true test of an artist’s dedication and craftsmanship.