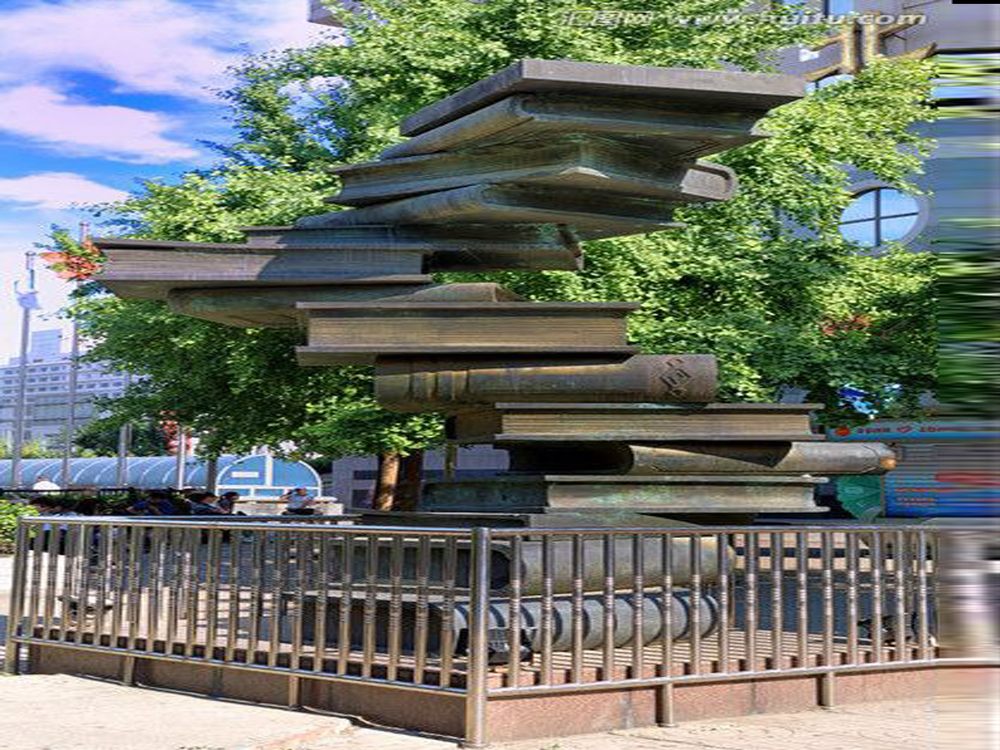
Creating porcelain sculptures with intricate geometries is a formidable challenge that demands both technical mastery and artistic vision. Artists employ a blend of traditional craftsmanship and modern innovations to bring these delicate works to life.
One key approach is modular construction, where complex forms are broken into smaller, manageable sections. These components are individually shaped, dried to a leather-hard state, and then meticulously joined using slip (liquid clay). This method reduces warping during firing while allowing for precise alignment of geometric patterns.
Advanced 3D printing technologies have revolutionized the field. Ceramic 3D printers extrude specially formulated porcelain clay layer by layer, enabling previously impossible geometries. Post-printing, artists refine surfaces and maintain structural integrity through controlled drying—often taking weeks—before kiln firing.
Traditional techniques remain vital. Press molds created from 3D-printed prototypes allow for reproduction of intricate designs, while slip casting facilitates hollow structures that minimize weight and cracking risks. Master artists also use computer-aided design to plan stress points and wall thicknesses before touching clay.
The final challenge is the kiln. Porcelain’s high shrinkage rate (up to 15%) requires precise calculation of geometries. Artists employ cone packs to monitor heat distribution and often fire sculptures at angles to prevent collapse. Some layer glazes strategically to reinforce fragile junctions.
Through this synergy of ancient wisdom and cutting-edge technology, contemporary ceramists continue pushing the boundaries of what’s possible in porcelain geometry—transforming mathematical precision into breathtaking art.