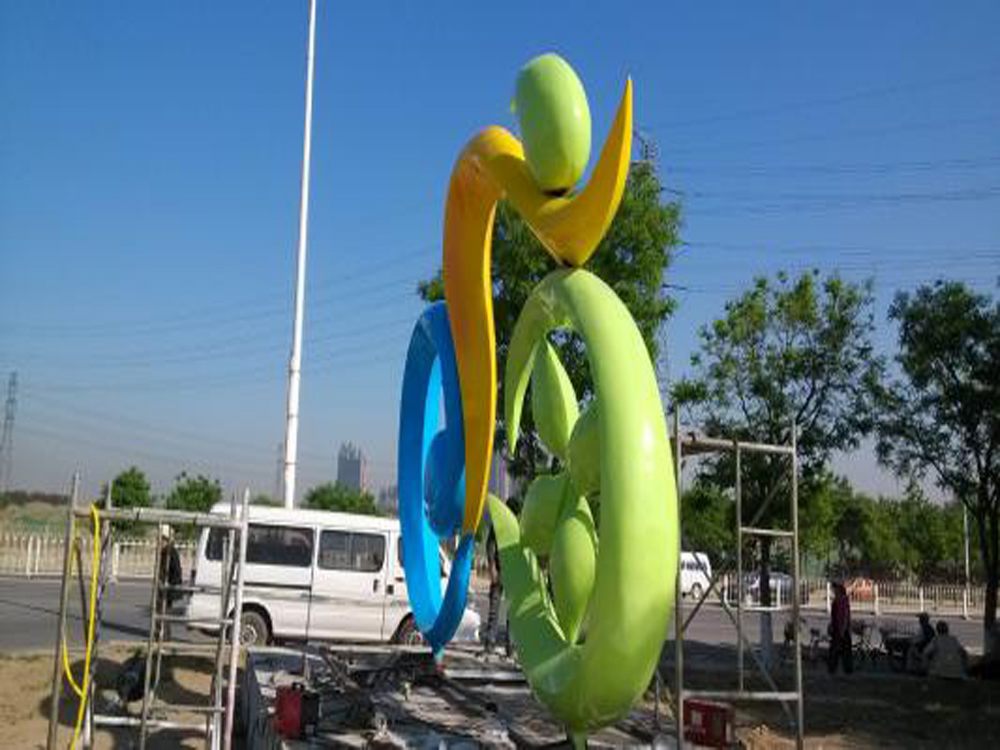
Creating large porcelain sculptures is a delicate dance between artistic vision and engineering precision. Artists must reconcile the inherent fragility of porcelain with the demands of monumental scale, employing innovative techniques to ensure both visual impact and longevity.
The foundation lies in material science. Many sculptors blend porcelain with additives like grog or paper fibers to enhance tensile strength while maintaining the material's luminous quality. Others use layered construction methods, building hollow forms with reinforced internal armatures that remain invisible to the viewer.
Form follows function in subtle ways. Experienced ceramicists incorporate organic curves and strategic thickness variations that distribute structural stress while creating dynamic visual flow. The Japanese technique of "neriage" – stacking colored clays – often gets adapted to create decorative patterns that also serve as structural reinforcement lines.
Firing presents another critical balancing act. Some artists employ multiple low-temperature bisque firings to gradually strengthen the piece before final glazing. Others experiment with saggar firing or alternative kiln atmospheres that produce stunning surface effects while minimizing warping risks in large works.
Contemporary innovators are pushing boundaries with hybrid approaches. 3D-printed porcelain scaffolds allow unprecedented precision in weight distribution, while some sculptors combine porcelain with metal or resin supports disguised as artistic elements. The most successful works make these technical solutions feel like inherent parts of the aesthetic statement – where every structural choice enhances rather than compromises the artistic vision.
Ultimately, mastering large porcelain sculpture requires equal parts potter's skill, architect's foresight, and artist's sensitivity – a rare convergence that transforms fragile clay into enduring art.