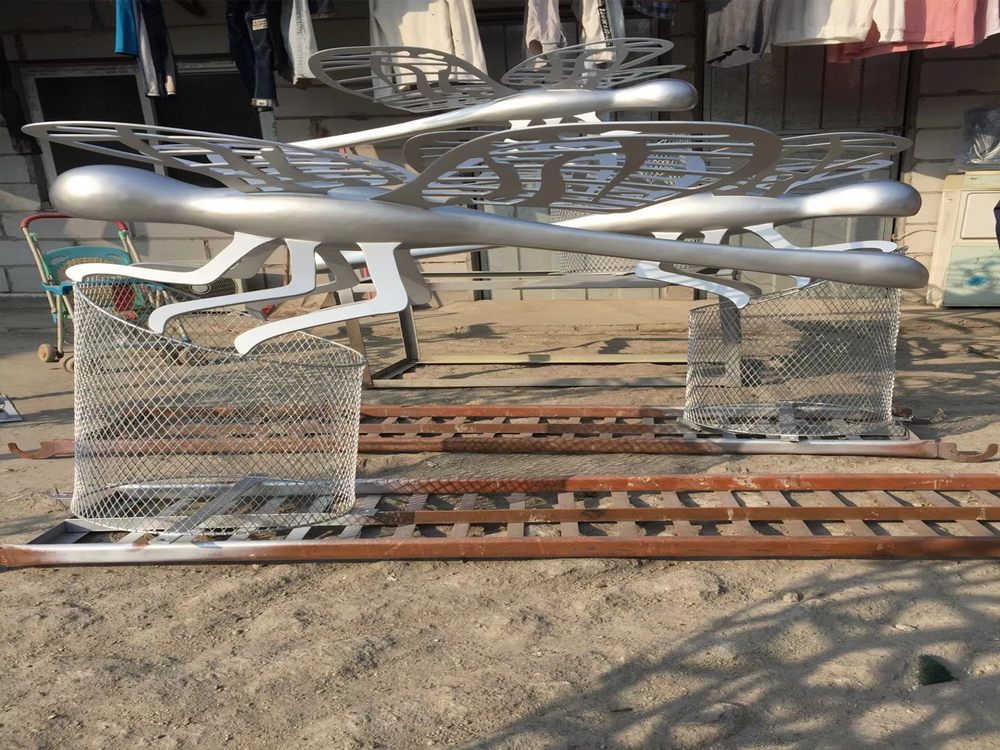
Achieving smooth gradient color effects in porcelain sculptures is a delicate art that requires meticulous technique and deep understanding of ceramic materials. Unlike canvas or paper, porcelain presents unique challenges due to its non-absorbent surface and the transformative nature of kiln firing.
Master artists employ several specialized methods to prevent bleeding and smudging:
1. Underglaze Layering: Artists apply multiple thin layers of underglaze colors, allowing each layer to dry completely before adding the next. This creates gradual transitions without color mixing.
2. Controlled Brushwork: Using fine brushes and precise strokes, artists blend colors while the underglaze is still slightly damp, working quickly to maintain clean edges.
3. Strategic Firing: The kiln temperature is carefully controlled during bisque firing (around 1000°C) to set the colors before the final glaze application.
4. Color Selection: Experienced artists choose underglazes with similar chemical compositions to ensure compatible melting points during firing.
5. Masking Techniques: Some artists use wax resist or tape to protect areas where sharp color divisions are required.
The final result emerges only after the high-temperature glaze firing (1200-1400°C), where the colors permanently fuse with the porcelain body. This complex process explains why gradient porcelain pieces command such admiration in the art world.