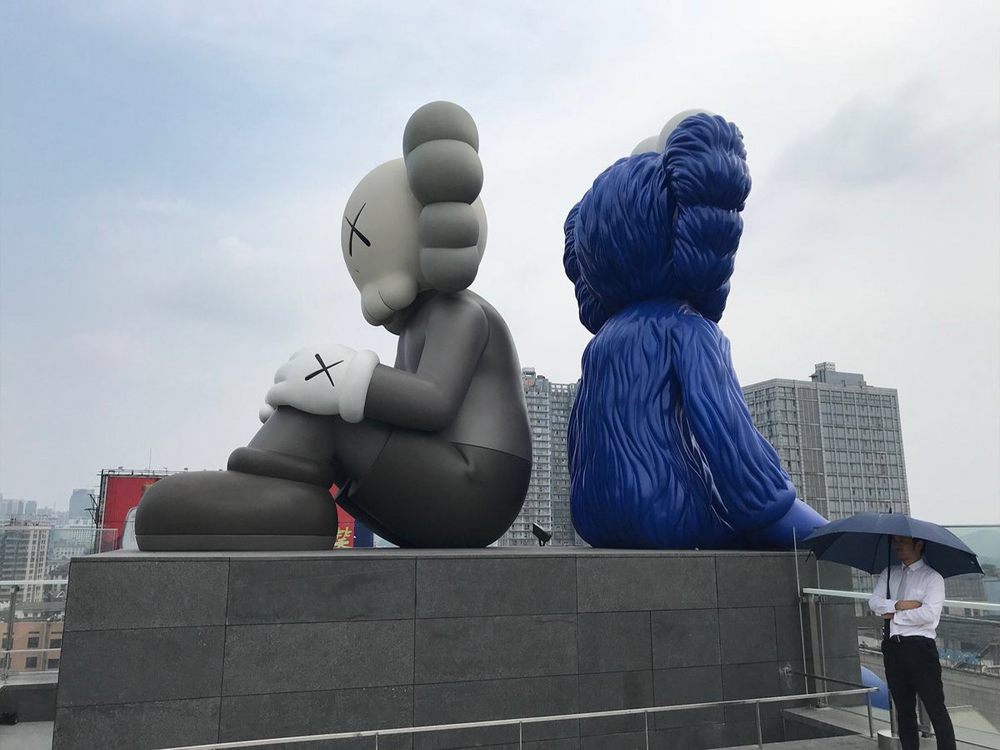
Creating porcelain sculptures with uniform wall thickness is a meticulous process that demands precision, skill, and specialized techniques. Artists employ several methods to ensure consistency, starting with the careful preparation of clay. Wedging the clay thoroughly removes air bubbles, which can cause uneven drying and cracking.
Many sculptors use calipers or thickness gauges to measure the clay walls at multiple points, ensuring uniformity before the piece dries. For hollow forms, artists often build sculptures in sections, allowing each part to dry evenly before assembly. Slip casting, a technique where liquid clay is poured into plaster molds, is another popular method for achieving consistent thickness in mass-produced pieces.
Experienced potters also rely on the "pinch and pull" technique, gradually shaping the clay while maintaining even pressure. Wheel-throwing is another approach, where centrifugal force helps distribute the clay uniformly. After shaping, slow and controlled drying prevents warping, followed by precise kiln firing to preserve the sculpture’s integrity.
Ultimately, mastering these methods requires years of practice, as even minor inconsistencies can lead to structural weaknesses or aesthetic flaws. Through patience and innovation, artists continue to push the boundaries of porcelain craftsmanship.