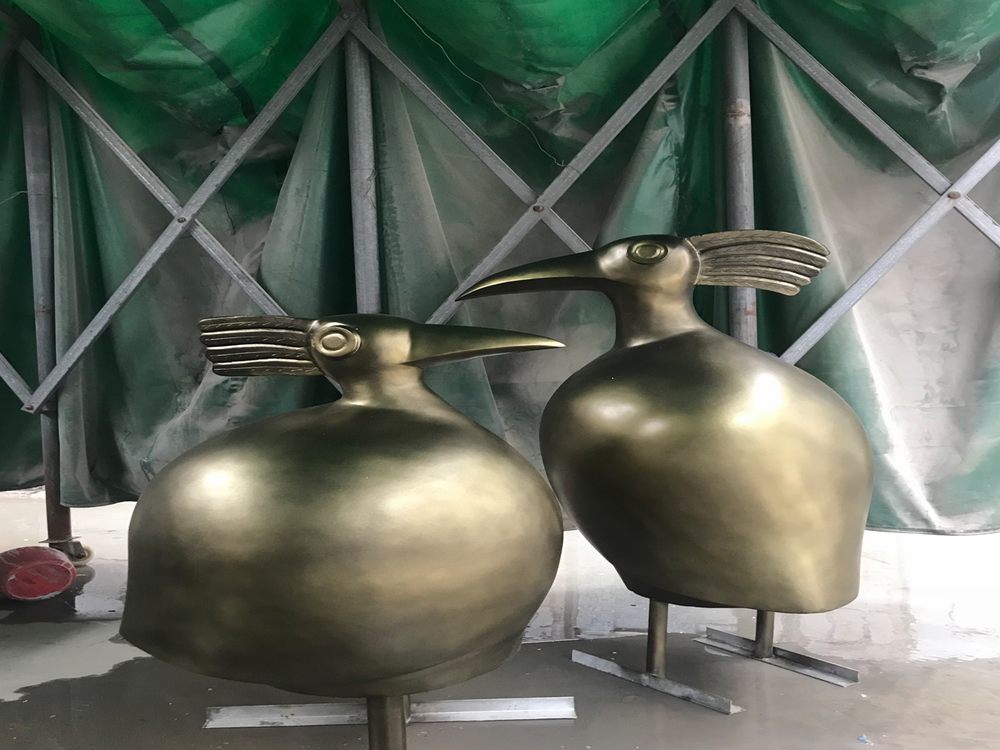
Creating porcelain sculptures that withstand extreme temperatures presents unique artistic and technical hurdles. One major challenge is material selection—standard porcelain may crack or warp under rapid temperature changes. Artists must experiment with specialized clay blends and additives to improve thermal shock resistance without compromising aesthetic qualities.
Another critical issue is structural integrity. Large or intricate sculptures face higher risks of stress fractures due to uneven heat distribution. Sculptors often design hollow forms or incorporate internal supports, but these solutions require precise engineering to avoid collapse during firing.
Glazing introduces further complexity. While glazes protect surfaces, their thermal expansion rates must perfectly match the clay body to prevent crazing or peeling. Achieving vibrant colors at high temperatures also limits pigment choices, as many conventional oxides degrade under extreme heat.
Perhaps the most unpredictable factor is kiln behavior. Even with advanced computer-controlled kilns, temperature fluctuations can cause catastrophic failures. Artists must master slow heating/cooling cycles and sometimes accept that certain designs simply won’t survive the firing process—a reality that pushes the boundaries of ceramic art.