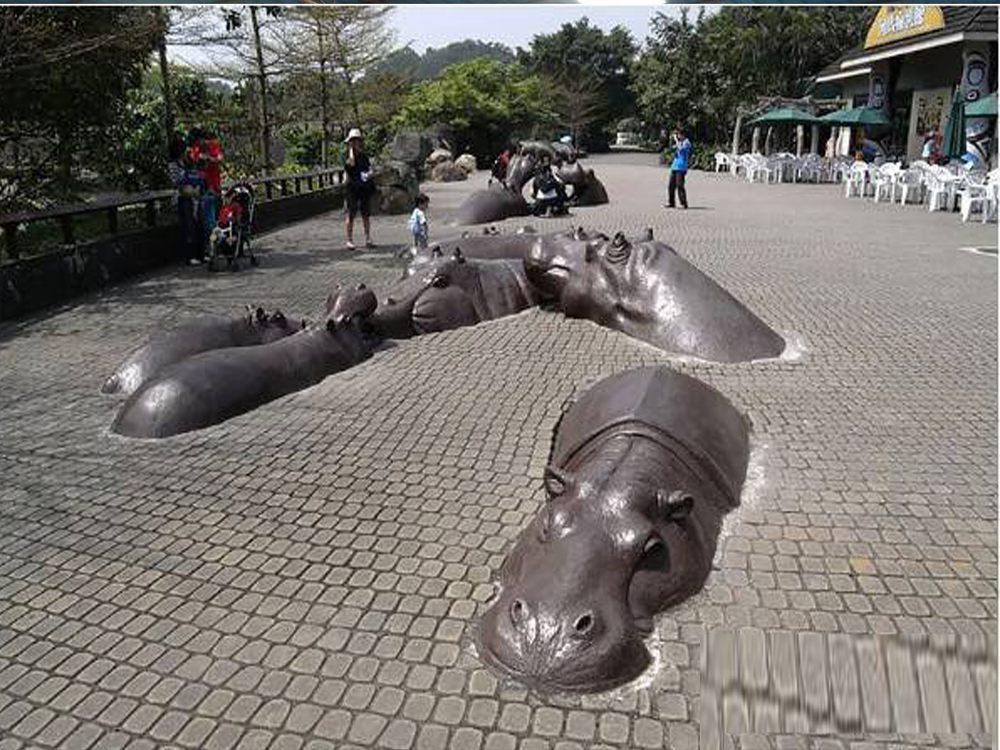
Bronze sculptures, whether displayed indoors or outdoors, showcase distinct differences in material composition and finishing techniques to suit their environments.
Material Composition:
Indoor bronze sculptures often use a purer bronze alloy (typically 90-95% copper with tin) for finer detailing and a smoother surface. Outdoor sculptures, however, incorporate additional metals like zinc or nickel (5-10%) to enhance durability against weathering. Some outdoor pieces may even include stainless steel cores for structural reinforcement.
Finishing Techniques:
Indoor sculptures frequently feature polished or gilded finishes to highlight intricate details in controlled lighting. A clear lacquer or wax coating preserves their original appearance with minimal maintenance. Outdoor bronzes undergo specialized patination processes, creating darker, textured surfaces like verdigris (greenish-blue) or brown-black finishes. These are often sealed with multiple protective layers, including microcrystalline wax or modern polymer coatings, to resist UV rays, acid rain, and temperature fluctuations.
Environmental Adaptations:
Outdoor sculptures incorporate design elements like drainage channels to prevent water pooling, while indoor pieces prioritize aesthetic refinement. Maintenance also differs—outdoor bronzes require periodic cleaning and re-waxing, whereas indoor pieces mainly need dusting.
Understanding these differences helps collectors and artists make informed decisions about placement, preservation, and artistic intent for bronze artworks.