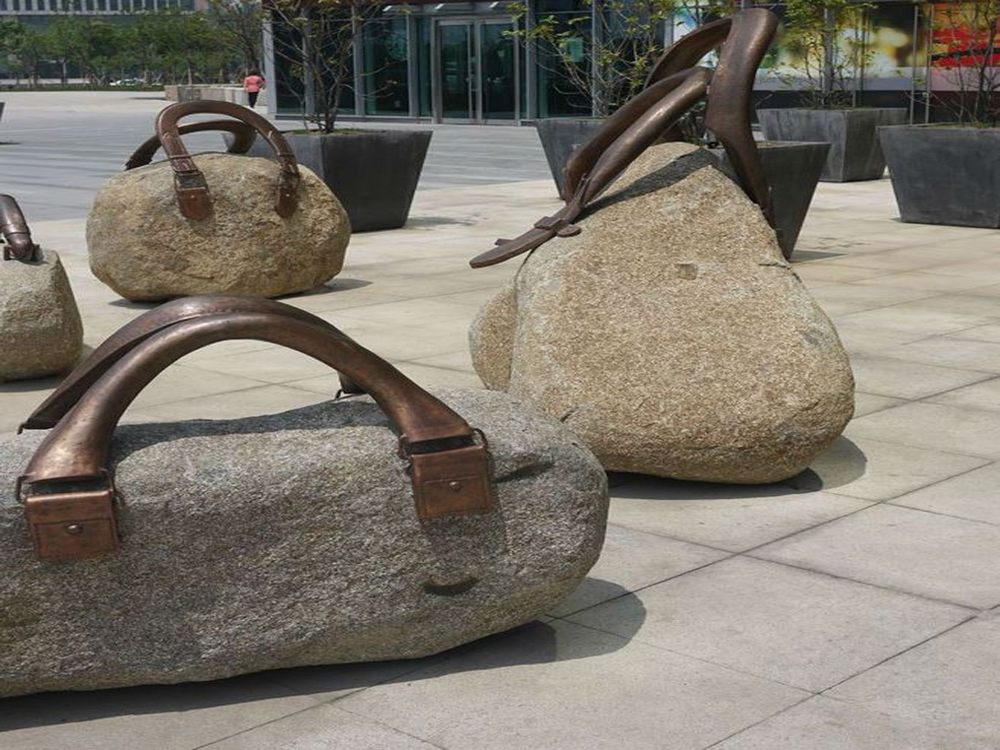
The wax modeling phase is a critical stage in bronze sculpture creation, bridging the artist's vision and the final metal casting. Here are the key steps involved:
1. Design Transfer: The artist begins by transferring the initial clay or digital design onto a wax medium. This involves carving or shaping the wax to match the intended sculpture.
2. Detailing & Refinement: Using specialized tools, the artist meticulously refines the wax model, adding intricate textures, patterns, or fine details that will be preserved in the bronze casting.
3. Spruing & Gating: Wax rods (sprues) and channels (gates) are attached to the model to create pathways for molten bronze to flow and for gases to escape during casting.
4. Investment Mold Preparation: The wax model is coated with a ceramic shell or plaster to form a mold. Once hardened, the wax is melted out (lost wax process), leaving a cavity for the bronze.
5. Final Inspection: Before casting, the wax model is carefully inspected for imperfections, ensuring the final bronze piece will accurately reflect the artist's vision.
This phase demands precision and creativity, as the wax model directly influences the quality and detail of the finished bronze sculpture.