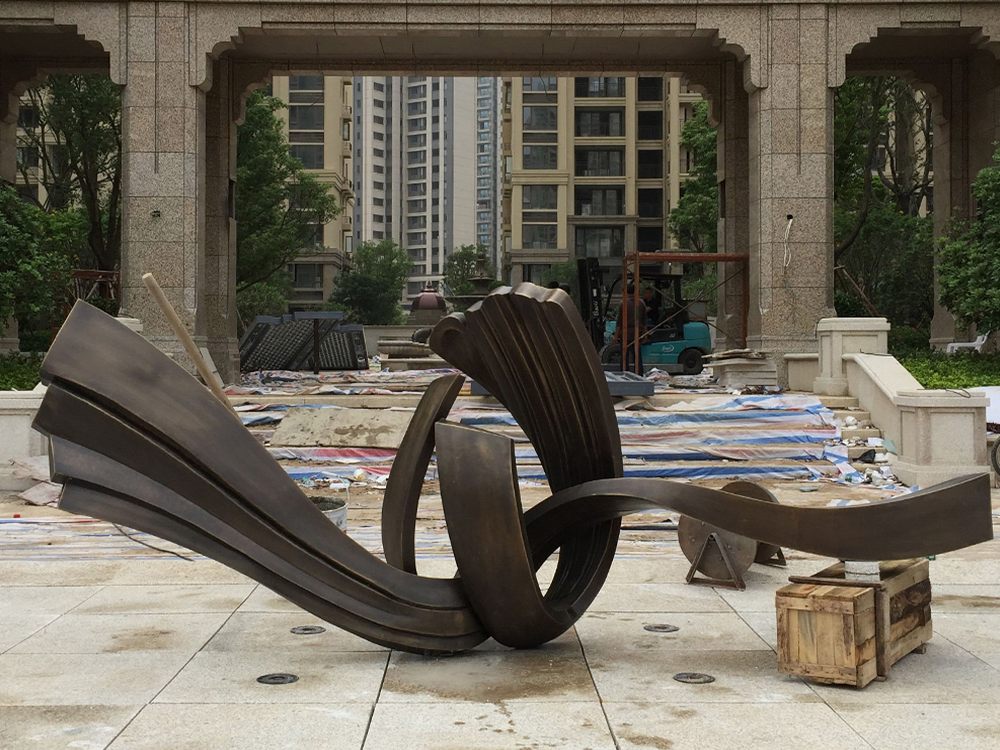
Bronze casting is an ancient and intricate process, but even skilled artisans encounter defects that can compromise the final product. Among the most common issues are porosity, shrinkage cavities, misruns, cold shuts, and inclusions.
Porosity occurs when gas bubbles become trapped in the metal, creating voids. This can be mitigated by proper mold venting, controlled pouring temperatures, and using degassing agents. Shrinkage cavities form as the metal cools and contracts; these are minimized through strategic riser placement and controlled cooling rates.
Misruns and cold shuts happen when molten bronze fails to fill the mold completely or solidifies prematurely. Maintaining adequate pouring temperatures and ensuring proper gating system design can prevent these flaws. Inclusions, caused by foreign particles in the metal, are avoided through careful metal preparation and filtration.
Modern foundries employ various techniques to address these challenges, including X-ray inspection for internal defects and specialized repair methods like welding or impregnation for salvageable pieces. Understanding these common defects and their solutions helps craftsmen produce higher quality bronze castings with greater consistency.