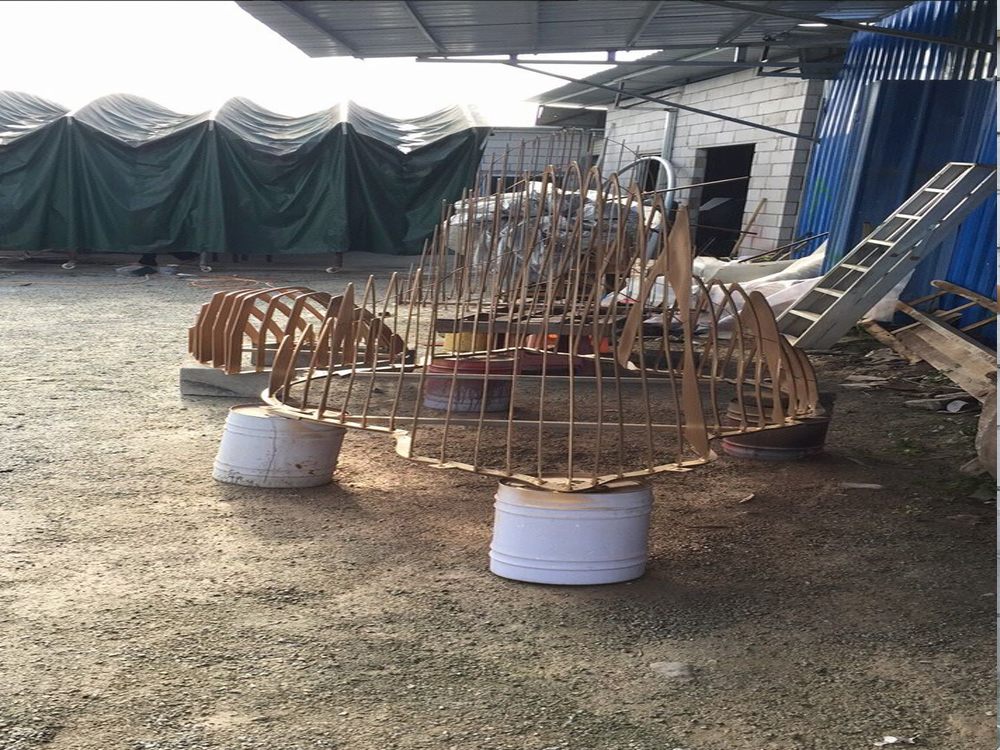
Bronze sculptures have long been revered as masterpieces of art, but they also serve as tangible records of technological progress in welding and metalworking. From ancient lost-wax casting to modern TIG welding, these artworks reveal the ingenuity of metal artisans across centuries.
The earliest bronze sculptures, dating back to 3000 BCE, relied on primitive joining methods like forge welding and riveting. Greek and Roman sculptors later refined these techniques, creating seamless joins that still awe conservators today. The Renaissance brought brazing innovations, allowing more intricate designs like Cellini's Perseus.
Modern welding breakthroughs transformed bronze sculpture in the 20th century. Oxyacetylene welding enabled larger installations, while arc welding techniques permitted abstract forms previously impossible to construct. Contemporary artists now combine MIG welding with 3D-printed molds, pushing boundaries of scale and complexity.
Beyond joining methods, bronze sculptures demonstrate advancements in metal preparation. Ancient patination formulas have given way to electrochemical treatments that create durable, vibrant surfaces. Modern alloys with precise copper-tin ratios offer improved workability and corrosion resistance.
Today's conservation techniques also reflect progress. X-ray fluorescence helps analyze historical pieces without damage, while laser cleaning preserves delicate surfaces. These methods inform both art restoration and industrial metalworking practices.
From Rodin's welded fragments to Anish Kapoor's monumental castings, bronze sculptures continue to be both artistic statements and technical demonstrations. They stand as enduring proof that art and engineering evolve in tandem, each driving the other forward through centuries of innovation.