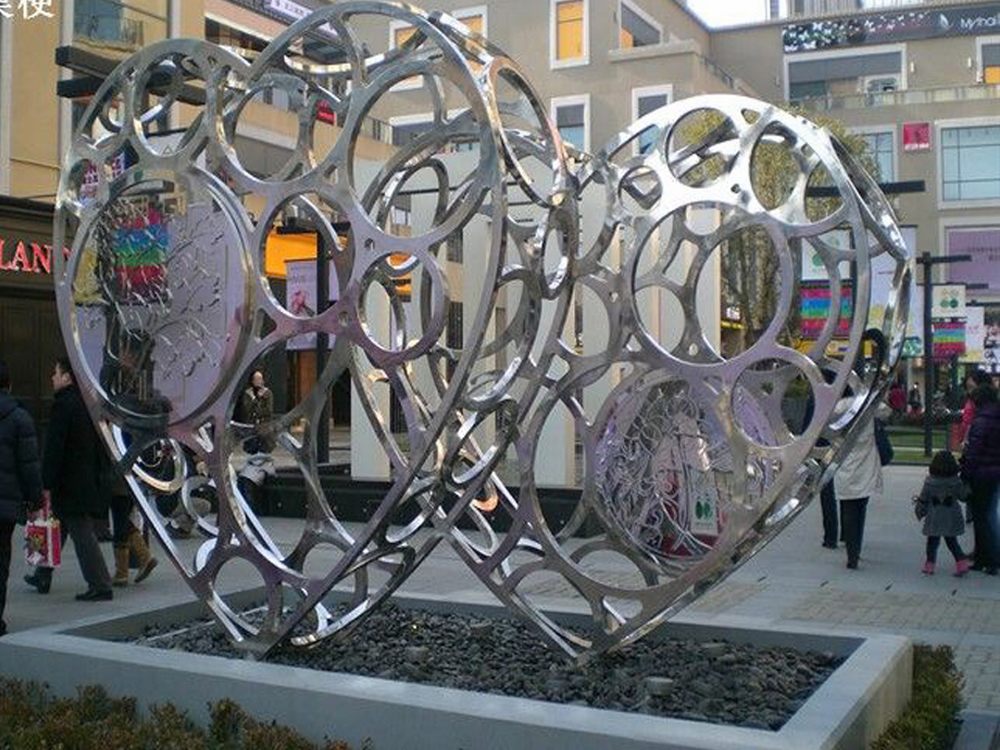
The creation of bronze sculptures during the Renaissance period followed dramatically different technical processes compared to contemporary methods. Renaissance artists like Donatello and Ghiberti relied heavily on the traditional lost wax (cire perdue) technique, where a clay core was covered in beeswax for modeling before being encased in fireproof material and melted away to create molds. This labor-intensive process often required entire workshops and produced thicker-walled castings with visible seams.
Modern bronze sculptors benefit from technological advancements like silicone mold-making, 3D printing for maquettes, and improved metal alloys. Contemporary artists frequently employ indirect casting methods, allowing for thinner walls, greater precision, and the ability to create editions. While Renaissance bronzes show hand-chased details and intentional oxidation patinas, modern pieces often feature experimental finishes like colored patinas or polished surfaces.
The Renaissance approach emphasized manual craftsmanship within strict guild systems, while today's artists combine traditional foundry work with digital tools and conceptual approaches. Both periods share the fundamental bronze casting principles, but modern techniques offer greater flexibility in scale, reproduction, and surface treatment while losing some of the tactile authenticity of Renaissance works.