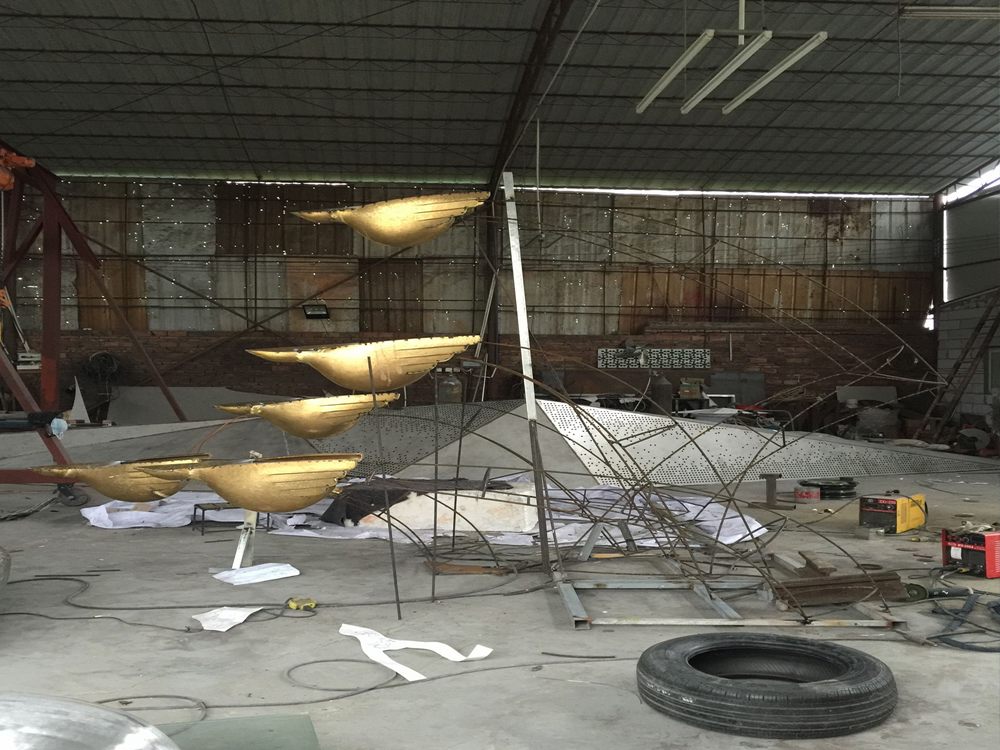
Bronze casting is a revered ancient art, but even experienced craftsmen encounter defects. The most common issues include porosity, shrinkage, cold shuts, and misruns.
Porosity occurs when gas becomes trapped in the metal, creating tiny bubbles. This can be prevented by proper venting of molds and controlling pouring temperature. For existing porosity, techniques like metal stitching or epoxy filling are effective solutions.
Shrinkage defects appear as cavities due to uneven cooling. Addressing this requires careful design of risers and gating systems to ensure proper metal flow. Preheating molds also helps maintain consistent cooling rates.
Cold shuts and misruns happen when molten metal fails to fuse properly, often due to low pouring temperatures or slow flow. Increasing metal temperature and optimizing mold design can prevent these flaws. For repairs, welding or brazing may be used on finished pieces.
Modern foundries employ X-ray and ultrasonic testing to detect hidden defects early. Many imperfections can be corrected through skilled chasing, patination, or strategic design modifications that incorporate flaws as artistic elements.
Prevention remains the best approach, with meticulous attention to mold preparation, metal composition, and controlled cooling processes. When defects do occur, understanding their causes allows for appropriate remediation while preserving the artwork's integrity.