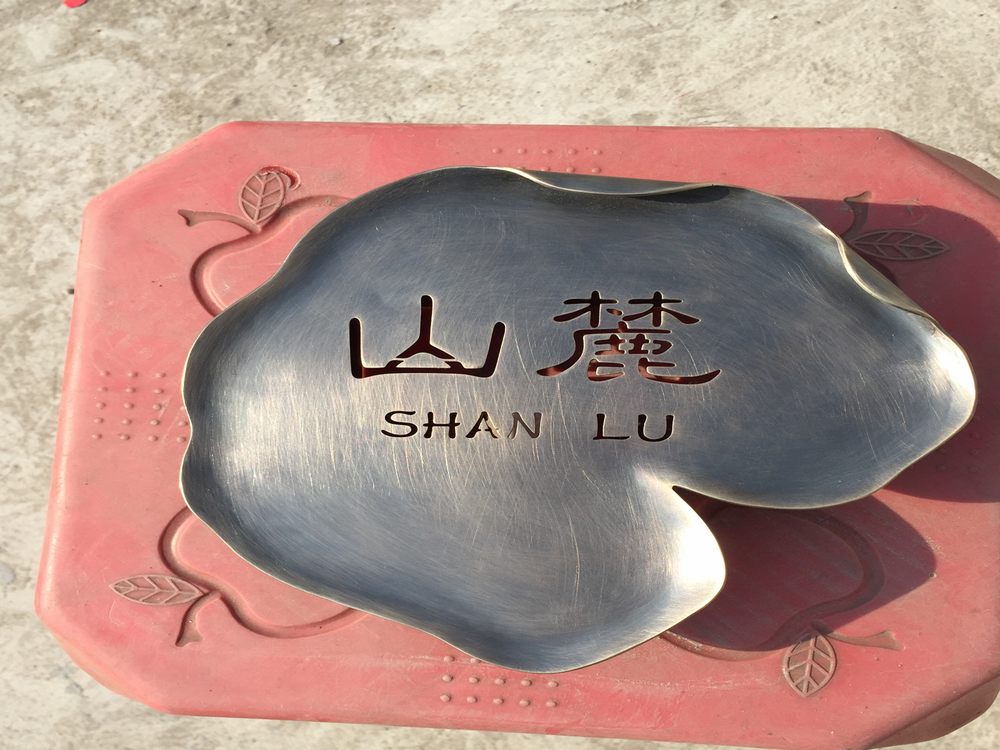
The foundry serves as the transformative bridge between an artist’s vision and a finished bronze sculpture, executing complex technical processes that demand both precision and craftsmanship. Using ancient techniques like lost-wax casting, foundries convert fragile clay or wax models into enduring metal artworks through a multi-stage alchemy.
First, the original sculpture is encased in silicone to create a detailed mold, which is then filled with wax to form a perfect replica. Artisans meticulously refine this wax version before surrounding it with ceramic shell material. During the burnout phase, the wax melts away, leaving a hollow cavity that becomes the mold for molten bronze poured at 2,000°F.
Modern foundries combine Renaissance-era methods with technological advancements, offering artists specialized services like:
- Patina chemistry for custom surface coloration
- Structural engineering for large-scale installations
- Metal alloy blending for specific durability needs
Beyond mere metal casting, foundries solve critical challenges – preventing bubbles in pours, compensating for metal shrinkage, and ensuring even wall thickness. This collaboration allows sculptors to focus on creative expression while relying on the foundry’s metallurgical expertise to preserve their work for centuries. The final bronze sculpture carries not just the artist’s signature, but the invisible craftsmanship of skilled foundry workers who mastered fire and metal to make art eternal.