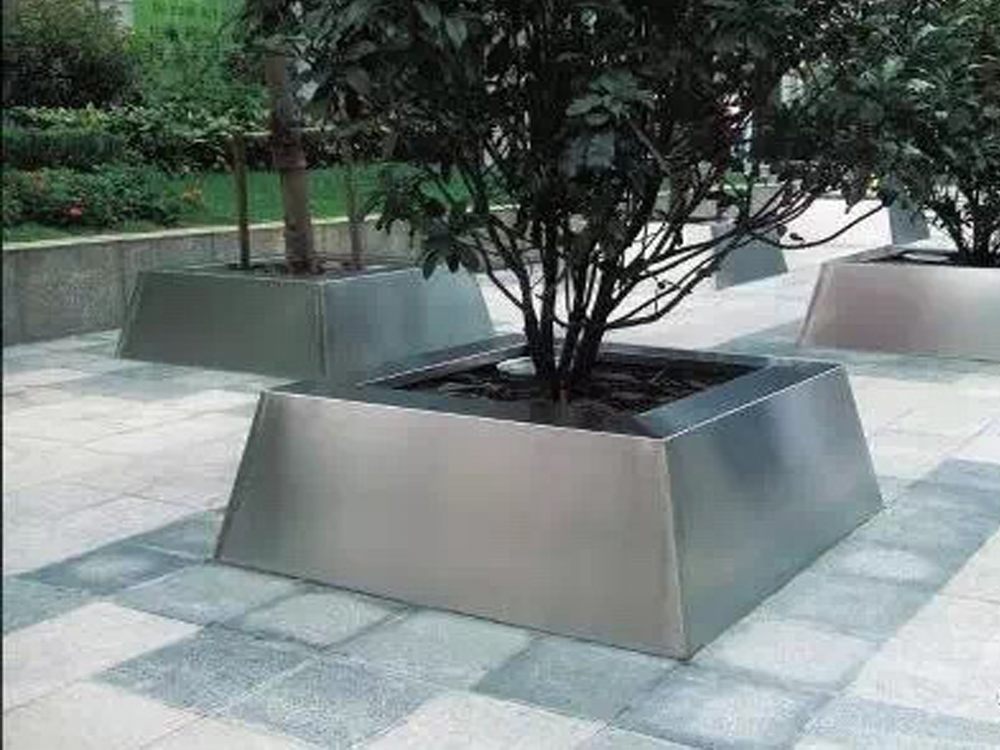
Creating bronze sculptures is a meticulous process, and gas holes—tiny cavities formed by trapped gas during casting—can compromise the artwork's integrity. To prevent these defects, follow these proven techniques:
1. Proper Mold Preparation: Ensure molds are thoroughly dried and preheated to eliminate moisture, a common source of gas formation.
2. Optimal Pouring Temperature: Maintain the bronze at the correct temperature—too hot increases gas solubility, while too cold causes premature solidification.
3. Degassing Agents: Use chemical degassers like phosphorus copper to remove dissolved gases from molten bronze before pouring.
4. Ventilation Channels: Design molds with adequate vents to allow gases to escape during casting, reducing trapped air pockets.
5. Slow, Controlled Pouring: Pour molten bronze steadily to minimize turbulence, which can introduce gas into the metal.
6. Post-Casting Inspection: Use X-rays or ultrasonic testing to detect hidden gas holes early, allowing for timely repairs.
By implementing these methods, artists and foundries can significantly reduce gas holes, ensuring durable, high-quality bronze sculptures. Regular practice and attention to detail are key to mastering flawless metal casting.