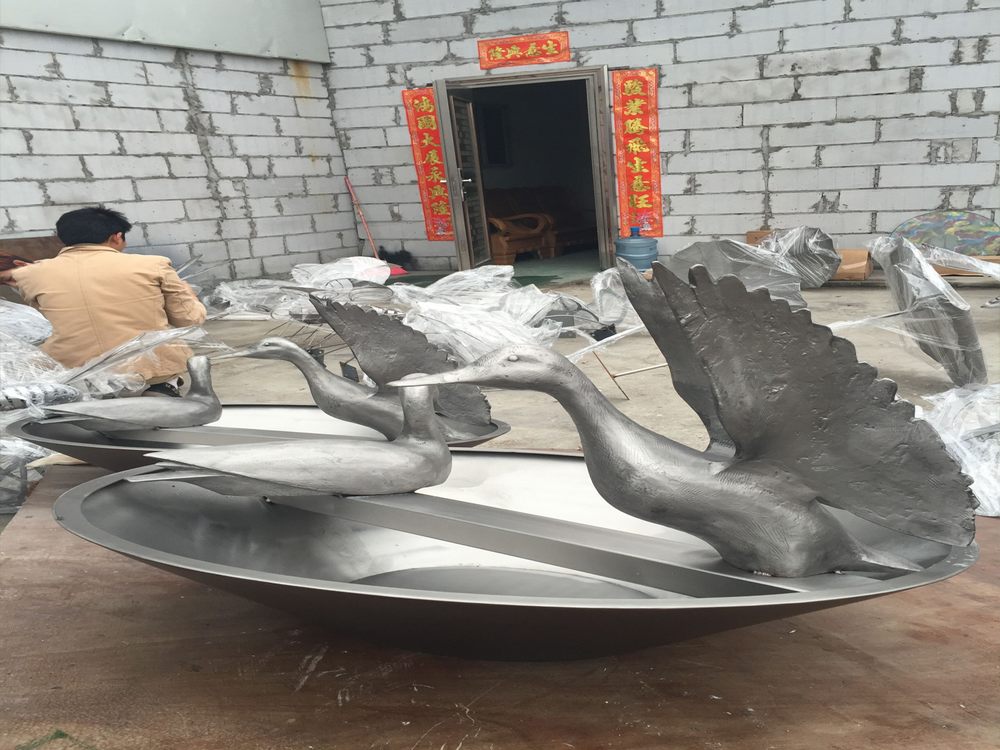
Creating large-scale bronze sculptures is a complex process that demands precision, engineering expertise, and artistic vision. Foundries employ a variety of techniques to ensure these monumental artworks remain structurally sound for generations.
One critical step is the use of high-quality materials. Bronze, an alloy of copper and tin, is chosen for its durability and malleability. Foundries carefully control the alloy composition to balance strength and workability, preventing cracks or weaknesses in the final piece.
Engineering plays a pivotal role. Sculptures are often designed with internal armatures—metal frameworks that provide stability. Advanced computer modeling helps simulate stress points, allowing engineers to reinforce vulnerable areas before casting begins.
The lost-wax casting method remains a gold standard. Artists create a detailed wax model, which is then encased in a ceramic shell. Molten bronze replaces the melted wax, capturing intricate details while maintaining structural integrity. For massive sculptures, sections are cast separately and welded together with precision.
Post-casting treatments further enhance durability. Heat treatments relieve internal stresses, while patinas protect against corrosion. Regular maintenance, including inspections and cleaning, ensures longevity.
By combining traditional craftsmanship with modern technology, foundries produce bronze sculptures that withstand time, weather, and physical stresses—preserving artistic legacy for centuries.