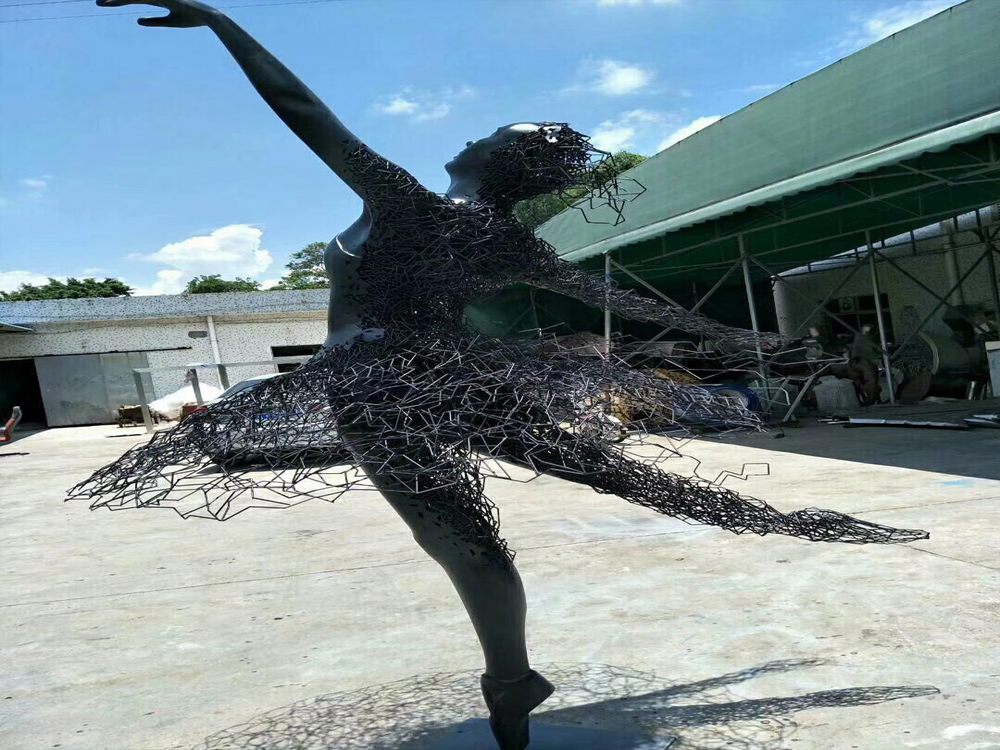
Bronze sculptures serve as timeless testaments to the metallurgical ingenuity of ancient civilizations, each culture imprinting its distinct techniques and artistic vision onto these enduring works. From the intricate lost-wax casting of West African Benin bronzes to the ceremonial precision of Chinese Shang dynasty vessels, these artifacts reveal far more than aesthetic mastery—they document the evolution of metalworking itself.
The Greeks perfected hollow casting methods that allowed for dynamic poses in their iconic statues, while Indian metallurgists developed advanced alloy compositions to achieve unparalleled durability in their Chola-era deities. Meanwhile, Mesoamerican cultures like the Mixtec created gold-like surfaces through specialized tumbaga alloys, demonstrating how material choices carried deep symbolic meaning.
What emerges across continents is a fascinating pattern: bronze technologies developed in response to local resources, spiritual beliefs, and functional needs. The thick-walled Zhou dynasty bells required different metallurgical solutions than the thin-walled Roman equestrian statues, with each culture's artisans solving these challenges through unique innovations in mold-making, alloy ratios, and finishing techniques.
Modern analysis of these sculptures reveals surprising sophistication—precise copper-tin ratios in ancient Indian bronzes show early understanding of material properties, while patination methods from different regions created signature surface effects. These artifacts thus form a material record of cultural exchange, with trade routes spreading both artistic styles and technical knowledge across civilizations.
Ultimately, studying these metallic masterpieces provides insight into how ancient societies transformed raw materials into cultural statements, with each hammer stroke and molten pour encoding centuries of accumulated metallurgical wisdom. The bronze that survived the ages carries not just artistic beauty, but the very fingerprints of human innovation.