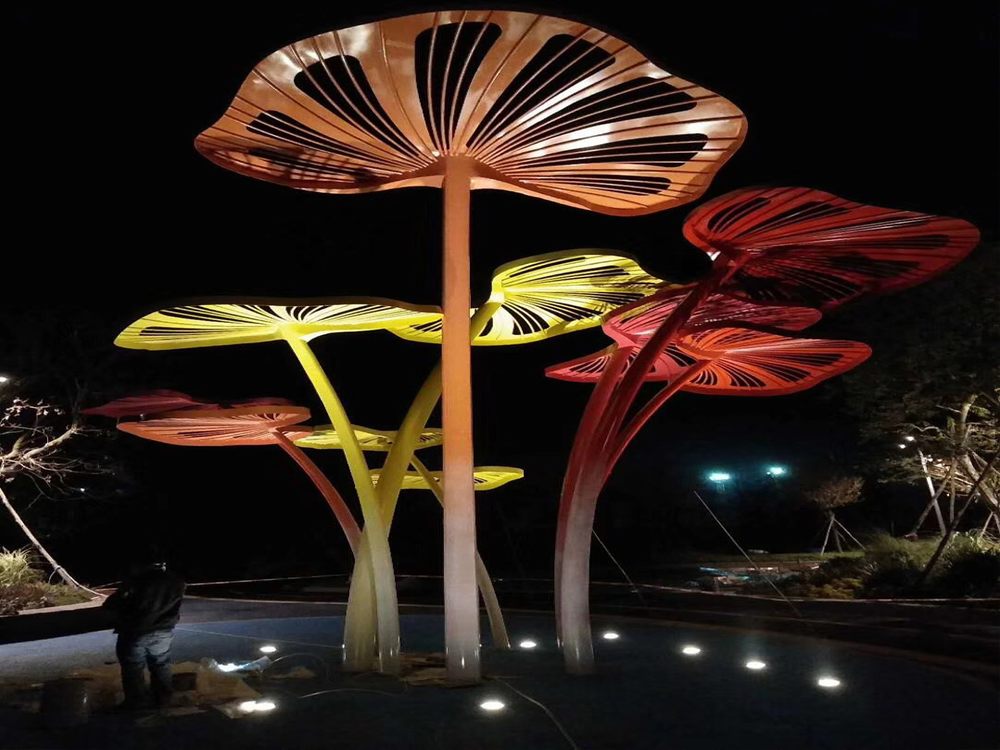
Gas venting is a critical aspect of the metal casting process, ensuring trapped gases escape to prevent defects like porosity or incomplete molds. Artists and foundries employ several techniques to manage this challenge effectively.
One common method is the use of vent holes or channels strategically placed in the mold. These vents allow gases to escape as molten metal fills the cavity, reducing pressure buildup. Foundries often design molds with porous materials, such as ceramic or specialized sand, which naturally permit gas diffusion.
Another approach involves the application of mold coatings or washes that enhance gas permeability. These coatings prevent metal penetration while allowing gases to pass through. In investment casting, wax patterns are coated with refractory materials that burn out during heating, leaving pathways for gas escape.
Advanced techniques include vacuum-assisted casting, where negative pressure pulls gases out before metal solidification. Some foundries also use inert gas flushing to displace oxygen and other reactive gases, minimizing oxidation and improving casting quality.
Artists working on smaller scales may rely on manual venting tools or carefully designed sprues that double as gas outlets. Proper venting not only improves structural integrity but also enhances surface finish, making it a vital consideration in both industrial and artistic casting.
By understanding and controlling gas behavior, professionals achieve cleaner, stronger castings with fewer imperfections, showcasing the intersection of science and craftsmanship in metalworking.