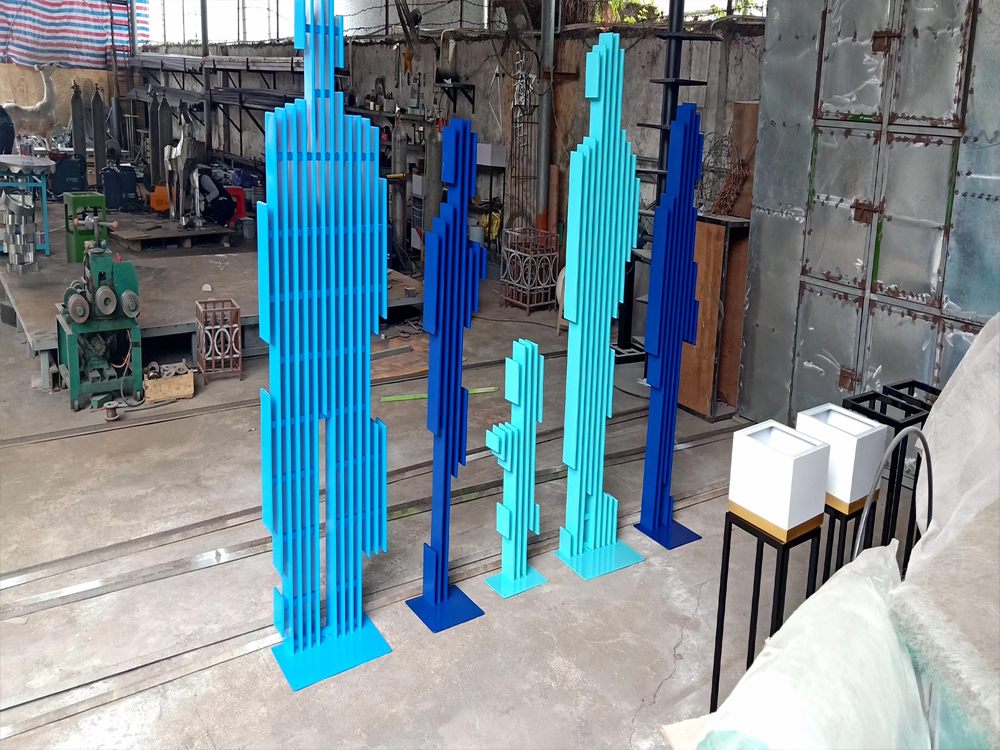
Creating identical coloration across multiple bronze editions requires meticulous attention to detail at every production stage. Artists begin by standardizing their alloy composition, as even minor variations in copper, tin, or zinc percentages can affect patina results. The crucial patination process involves precisely timed chemical applications - typically using ferric nitrate, cupric nitrate, or sulfur-based compounds - with each piece undergoing identical treatment durations under controlled temperature conditions.
Master artisans often create detailed color formulas documenting exact chemical mixtures, application methods, and heating protocols. Many employ test plates as references before treating final pieces. The finishing stage includes uniform waxing or lacquering to seal and protect the patina, with artists frequently applying multiple thin layers rather than single heavy coatings for consistency.
Environmental factors play a significant role - humidity, temperature, and even seasonal variations can impact results. Professional studios maintain climate-controlled patina areas and schedule editions during similar weather conditions. Some artists now use digital color-matching technology to verify hue consistency across editions, comparing spectral reflectance measurements to ensure perfect matches.
Through this combination of material science, chemical expertise, and environmental control, artists can reproduce identical bronze coloration even years apart, maintaining the integrity of limited edition series. The most successful practitioners document every variable, creating reproducible systems that withstand the test of time and multiple casting batches.