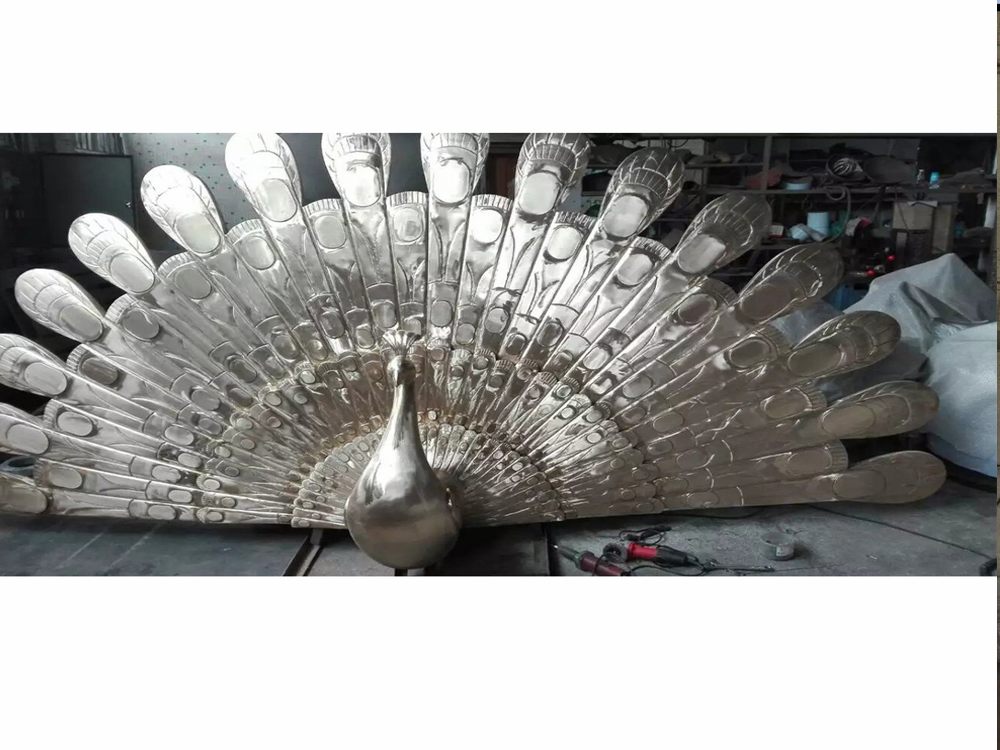
Achieving uniform color across bronze editions requires meticulous attention to patina chemistry, material consistency, and environmental control. Professional sculptors begin by standardizing their bronze alloy composition, as even minor variations in copper, tin, or zinc content can alter oxidation results. The patination process itself demands scientific precision - artists carefully measure chemical solutions (typically ferric nitrate, cupric nitrate, or sulfur-based compounds) and document application times down to the second.
Temperature and humidity control proves equally crucial, with many artists maintaining dedicated patina rooms where they can replicate identical atmospheric conditions for each piece. Some apply heat torching in consistent patterns to create predictable oxidation effects. Between editions, they clean bronze surfaces identically using matching abrasive techniques and chemical baths.
Experienced foundries often create "master patina samples" as reference guides, comparing each new piece under controlled lighting. Advanced practitioners may use spectrophotometers to measure color values numerically. The final protective wax or lacquer coating must also be applied with identical thickness and composition to preserve color integrity.
Contemporary artists increasingly document their entire process through video recording or detailed logs, enabling exact replication across editions. Some even reserve batches of patina chemicals from the same manufacturing lot to ensure consistency. These rigorous methods allow limited edition bronzes to maintain collector value through perfect visual harmony, despite being cast months or years apart.