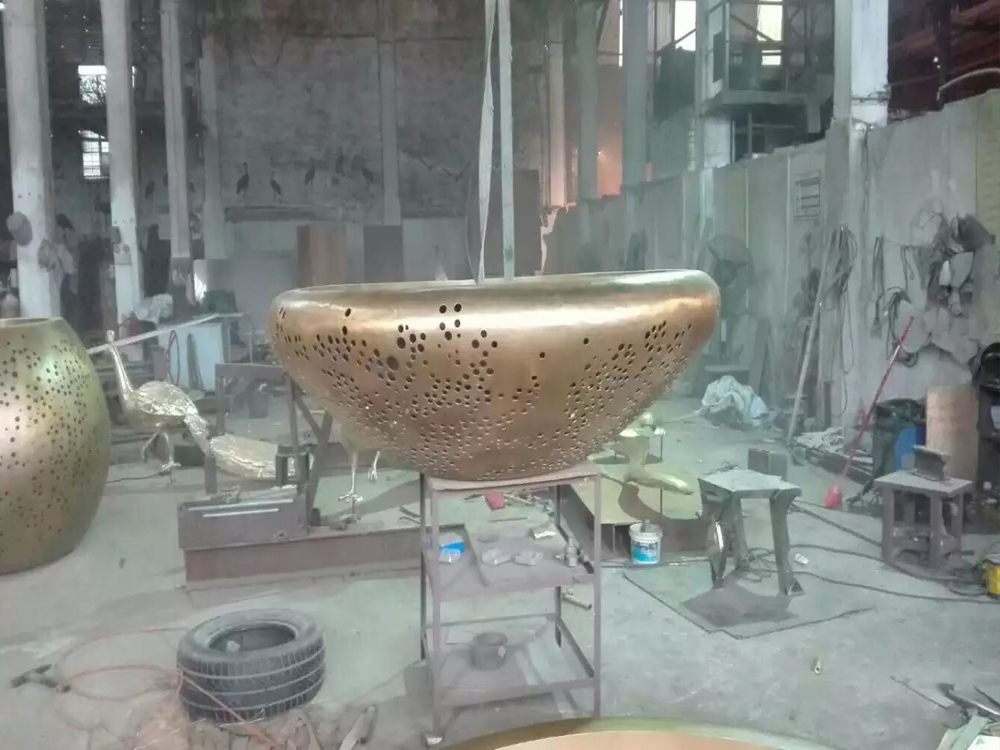
Bronze casting is one of the oldest and most respected metalworking techniques, with solid and hollow methods offering distinct advantages for different applications. The primary difference lies in their construction: solid bronze casting creates a completely dense metal object, while hollow casting produces a shell-like structure with an empty interior.
Solid bronze casting involves pouring molten bronze into a mold until completely filled, resulting in a heavy, durable piece ideal for small sculptures or functional items. This method provides excellent structural integrity but requires more material, making it more expensive. The weight of solid bronze works limits their size for practical display purposes.
Hollow bronze casting, developed by ancient Greeks, uses a clay core within the mold to create empty space. Modern techniques often employ the lost-wax process, where a wax model is melted away to form the cavity. This approach significantly reduces weight and material costs while allowing for larger sculptures. However, hollow castings may require internal supports for stability.
Artists choose between these techniques based on project requirements. Solid casting suits detailed small works needing durability, while hollow casting enables monumental sculptures. Contemporary foundries often combine both methods, using solid sections for strength with hollow areas to manage weight. Understanding these differences helps collectors and artists make informed decisions about bronze artworks.