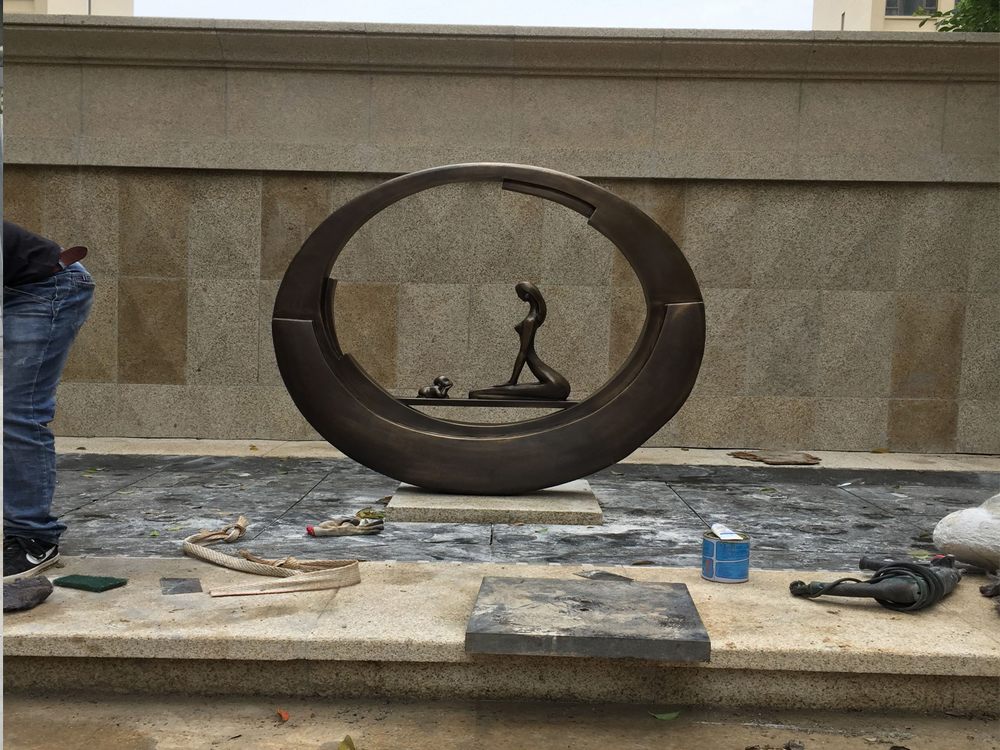
Creating bronze sculptures with internal support frameworks requires a blend of artistry and engineering. One of the most widely used methods is the lost-wax casting process, where a wax model is encased in ceramic, melted away, and replaced with molten bronze. This technique often incorporates internal metal armatures to provide structural stability during casting.
For larger sculptures, welded steel frameworks are essential. Artists construct these armatures to bear the weight of the bronze while allowing for dynamic poses. The framework must account for thermal expansion during casting and long-term environmental stresses.
Direct metal construction is another approach, where sculptors build up bronze sheets over an internal skeleton. This method offers more control over thickness and weight distribution. Many contemporary artists combine techniques, using 3D-printed frameworks with traditional bronze casting for complex geometries.
Proper framework design prevents cracking and distortion, ensuring the sculpture's longevity. The choice of technique depends on the sculpture's size, complexity, and the artist's preferred working methods. Mastering these approaches allows sculptors to push the boundaries of bronze as a medium while maintaining structural integrity.