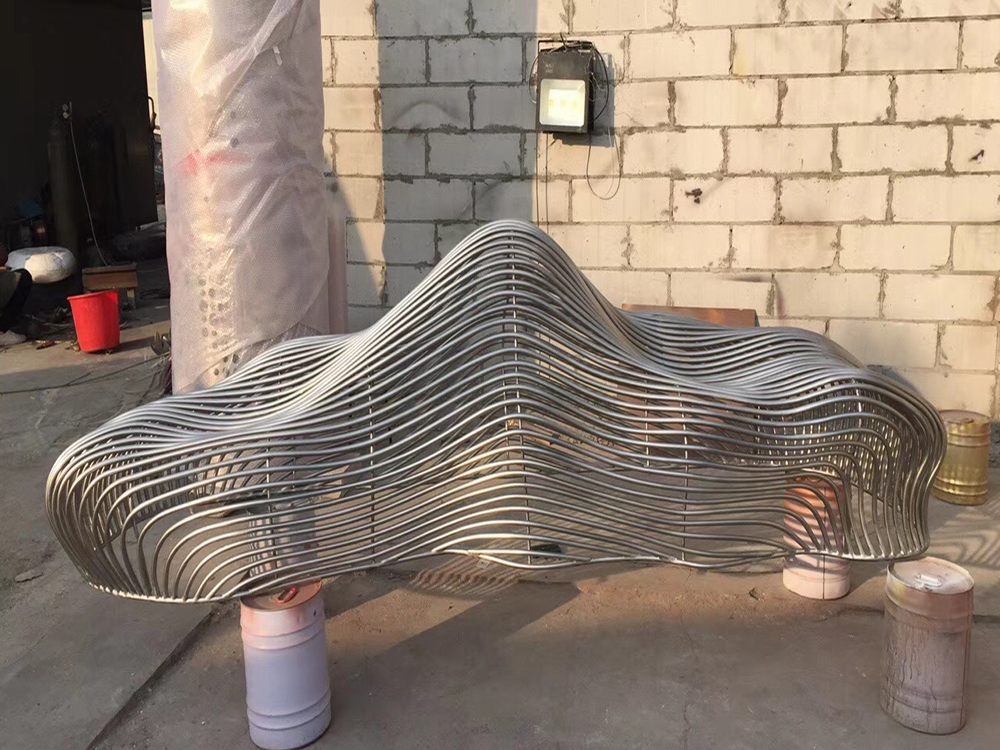
Bronze sculptures with projecting delicate elements, such as outstretched limbs or intricate details, require meticulous planning and advanced techniques to ensure structural stability. Artists employ several methods to achieve this, starting with a robust internal armature. This framework, often made of steel or reinforced metal, provides the necessary support to prevent sagging or breaking under the sculpture's weight.
The casting process itself is critical. Using the lost-wax method, artists create precise molds that account for the sculpture's weight distribution. Thicker sections of bronze are strategically placed near the base or connection points to reinforce weaker areas. Additionally, post-casting treatments like annealing—a controlled heating and cooling process—enhance the metal's durability.
For particularly fragile projections, artists may integrate hidden supports or braces, seamlessly blending them into the design. Environmental factors, such as wind or vibration, are also considered, with some sculptures featuring counterweights or flexible joints to absorb stress.
Finally, regular maintenance, including cleaning and inspections, ensures long-term stability. By combining engineering principles with artistic vision, sculptors create breathtaking bronze works that stand the test of time.