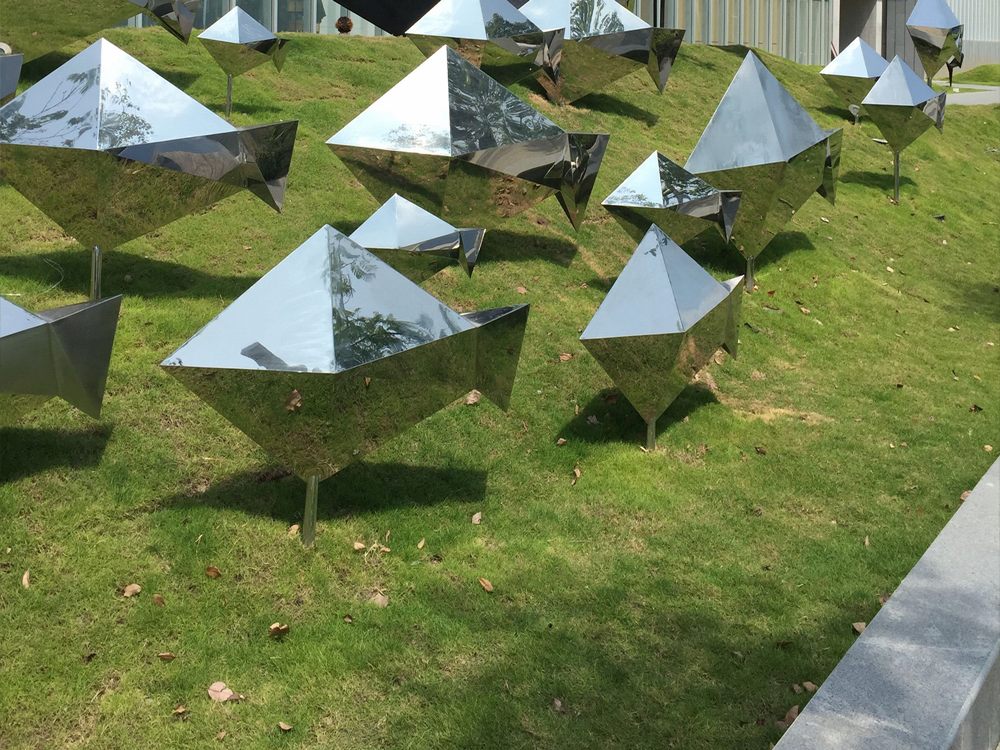
Bronze casting is a delicate art form where even minor flaws can ruin a masterpiece. One common challenge artists face is gas porosity—tiny bubbles trapped in the metal that weaken the structure and mar the surface. To prevent this, skilled artisans employ several proven techniques.
First, proper mold preparation is critical. Artists ensure molds are thoroughly dried and preheated to eliminate moisture, a major source of gas. Using vent channels in the mold design allows trapped air to escape during pouring.
The alloy mixture also plays a role. Experienced casters often add small amounts of deoxidizers like phosphorus copper to the molten bronze, which helps reduce gas formation. Maintaining optimal pouring temperature (typically between 1,100-1,200°C) prevents rapid cooling that can trap gases.
During pouring, artists use a steady, controlled stream to minimize turbulence. Some employ vacuum casting or centrifugal casting methods that actively remove air pockets. Post-casting, slow cooling in insulating materials gives remaining gases time to dissipate.
By combining these methods with meticulous attention to detail, artists consistently produce bronze works free from porosity defects—preserving both the beauty and structural integrity of their creations.