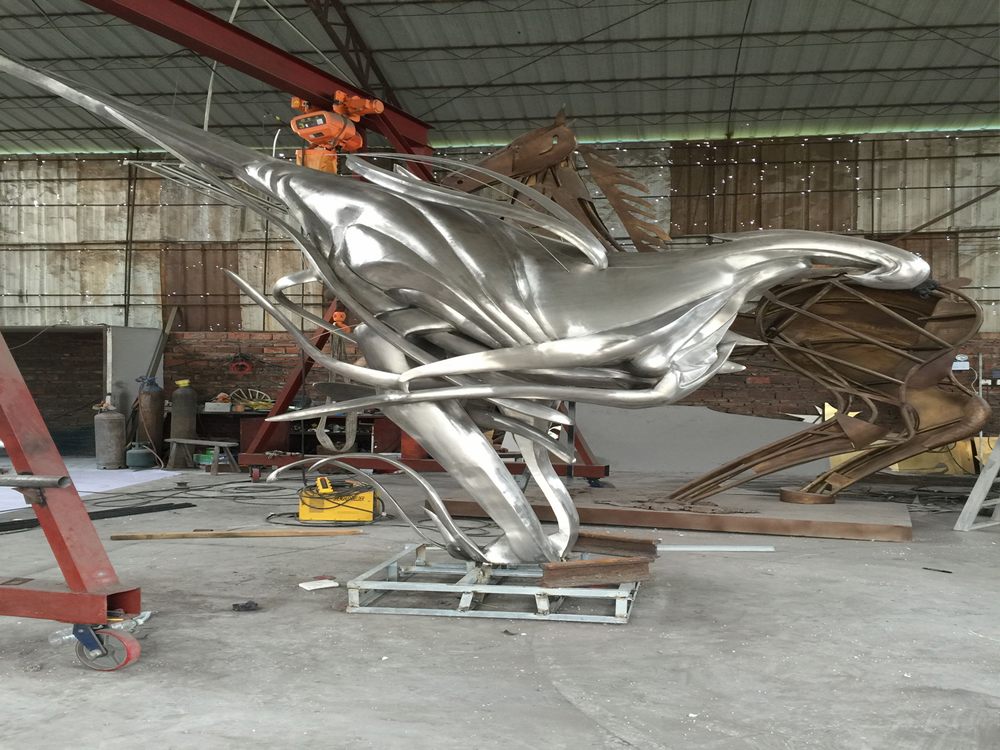
Annealing serves as a vital thermal process in bronze sculpture creation, fundamentally transforming the metal's properties at key stages. This controlled heating and gradual cooling technique performs three essential functions that distinguish professional bronze work.
During the initial casting phase, annealing relieves internal stresses that naturally develop as molten bronze solidifies in molds. The process involves heating the metal to approximately 1300°F (700°C) followed by slow cooling, which realigns the crystalline structure without melting the piece. This structural realignment prevents future cracking and warping that could compromise the sculpture's integrity.
For sculptors working with bronze sheets or rods, annealing restores malleability between hammering sessions. The metal work-hardens during shaping, becoming brittle and resistant to further manipulation. By periodically annealing the piece, artists can continue detailed forming without risking fractures, enabling intricate designs impossible with untreated bronze.
The final annealing stage occurs before patination, ensuring even chemical reactions across the entire surface. This thermal treatment creates uniform porosity in the metal, allowing patinas to develop consistent coloration and adhesion. Properly annealed sculptures maintain their artistic finish for generations, resisting environmental degradation far better than unannealed counterparts.
Contemporary sculptors combine traditional annealing methods with modern temperature controls, but the core principles remain unchanged since ancient times. This ancient technique continues to separate amateur attempts from professional bronze artworks, proving that some metallurgical wisdom withstands both time and technological advancement.