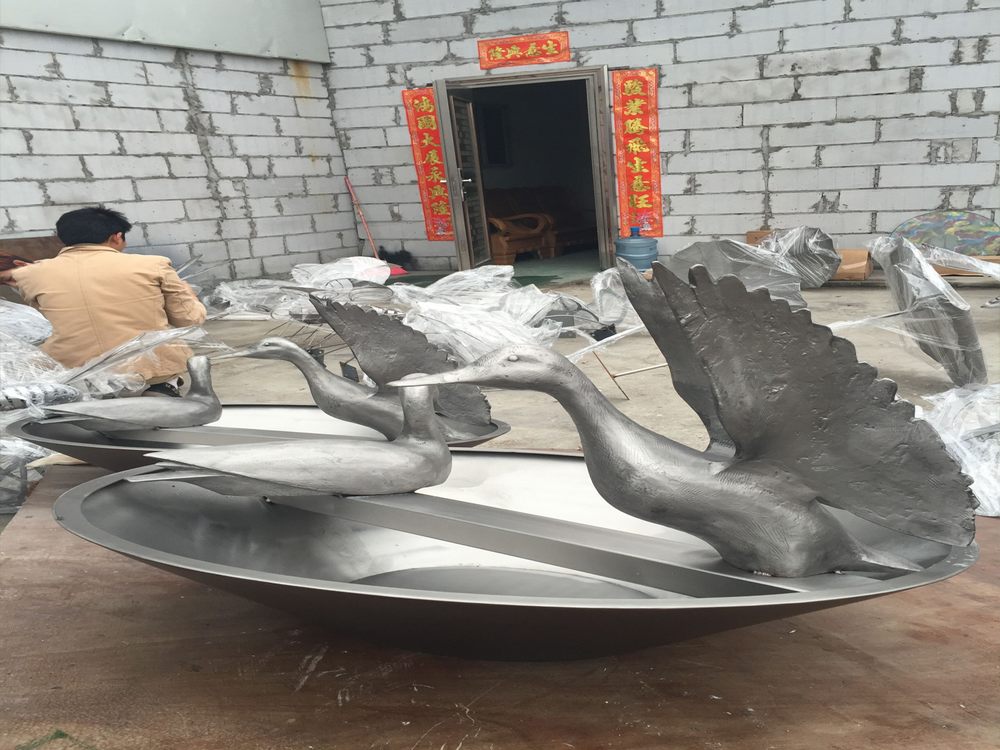
Creating a mirror-like polish on bronze sculptures is a meticulous process that combines artistry and technical skill. Artists begin by carefully sanding the bronze surface with progressively finer grits of sandpaper, often starting with coarse 80-grit and moving up to ultra-fine 2000-grit. This removes imperfections and creates a smooth foundation.
Next, buffing wheels with specialized compounds like rouge or tripoli are used to further refine the surface. The high-speed friction generates heat, helping to melt and smooth microscopic irregularities. Some artists employ electroplating techniques to deposit an ultra-thin layer of chrome or nickel for enhanced reflectivity.
Chemical patinas play a crucial role in achieving depth while maintaining shine. Artists may apply ferric nitrate or cupric nitrate solutions, carefully controlling the reaction time to create translucent layers that don't obscure the polished surface. The final step involves applying protective coatings like clear lacquer or wax to preserve the mirror finish from oxidation and environmental damage.
Modern sculptors sometimes incorporate power tools with felt or muslin attachments for consistent results, while traditionalists prefer hand-rubbing techniques that allow for nuanced control. The entire process can take weeks for large pieces, requiring patience and an unwavering attention to detail to achieve that perfect, reflective surface.