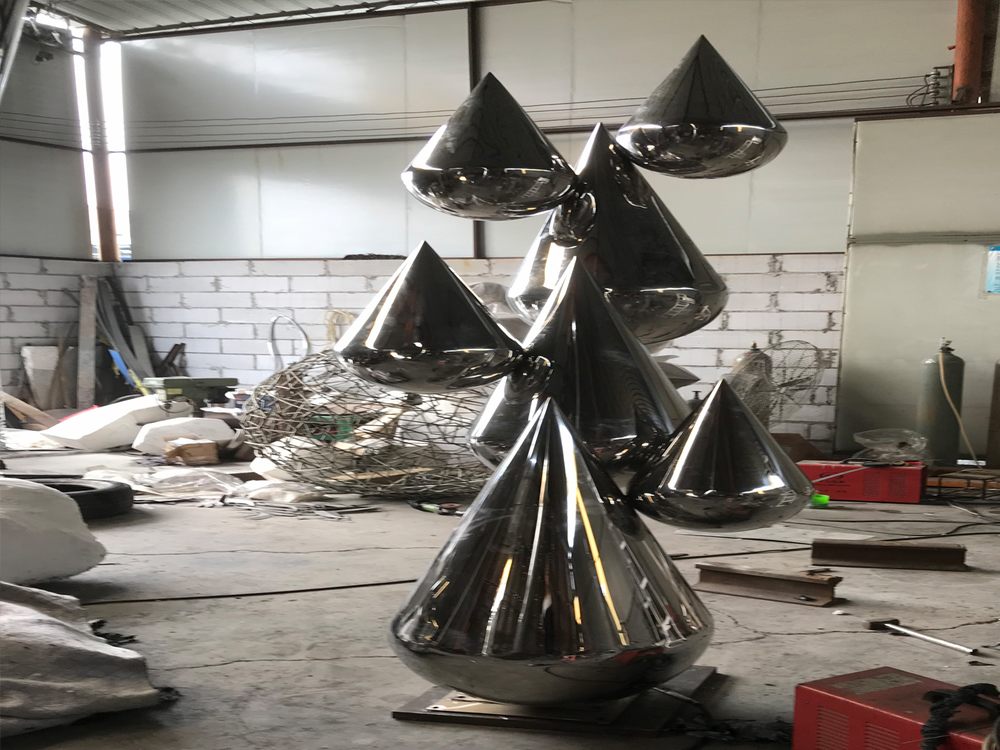
Bronze castings are widely used in industries ranging from art to engineering due to their durability and aesthetic appeal. However, several common defects can compromise their quality. Understanding these issues and implementing preventive measures is crucial for producing flawless bronze castings.
1. Porosity (Gas Porosity and Shrinkage Porosity)
Porosity occurs when gas bubbles form during casting or when the metal shrinks unevenly. To avoid this, ensure proper venting in molds, use degassing agents, and maintain consistent pouring temperatures.
2. Cold Shuts
Cold shuts happen when molten bronze streams fail to merge properly, creating weak seams. This can be prevented by increasing pouring temperatures, improving mold design, and ensuring smooth metal flow.
3. Misruns
Misruns occur when the bronze solidifies before filling the mold completely. Solutions include preheating molds, optimizing pouring speed, and using higher-temperature alloys.
4. Inclusions
Non-metallic particles trapped in the casting weaken its structure. Proper filtering of molten bronze and maintaining clean crucibles and molds can minimize inclusions.
5. Cracks (Hot Tears and Cold Cracks)
Rapid cooling or uneven solidification leads to cracks. Controlled cooling rates, stress-relief annealing, and alloy adjustments help prevent cracking.
By addressing these defects through careful process control, material selection, and mold design, manufacturers can produce high-quality bronze castings with superior strength and appearance. Regular inspections and quality checks further ensure defect-free results.