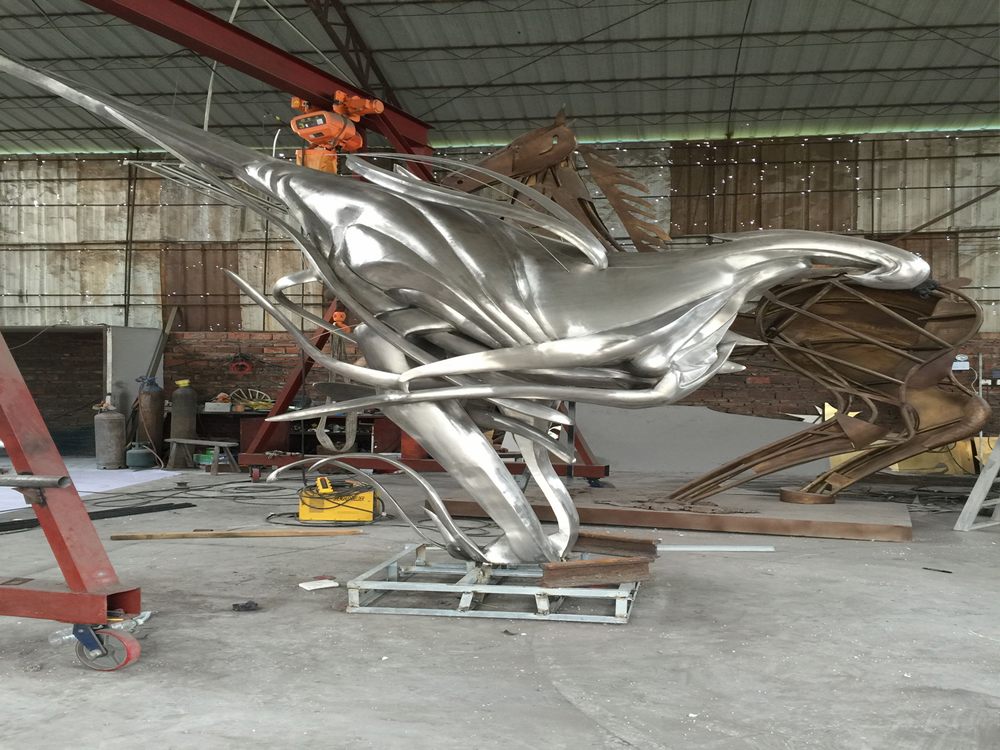
Bronze has been a favored medium for sculptors for centuries, prized for its durability and malleability. Yet, achieving a balance between longevity and artistic vision requires meticulous craftsmanship. Artists begin by selecting high-quality bronze alloys, often blending copper with tin or other metals to enhance strength while preserving workability.
The lost-wax casting method is a cornerstone technique, allowing intricate designs to be captured in metal. Artists first sculpt their vision in wax, which is then encased in a ceramic mold. Once the wax is melted away, molten bronze is poured into the cavity, solidifying into a detailed, durable form. This process enables delicate textures and dynamic compositions without sacrificing structural integrity.
Patination, the application of chemical treatments, adds another layer of artistic control. By manipulating oxidation, artists introduce rich hues—from deep greens to warm browns—enhancing visual appeal while protecting the surface from corrosion.
Ultimately, the synergy of material science and creativity empowers artists to craft bronze sculptures that endure both physically and aesthetically, standing the test of time while captivating viewers.