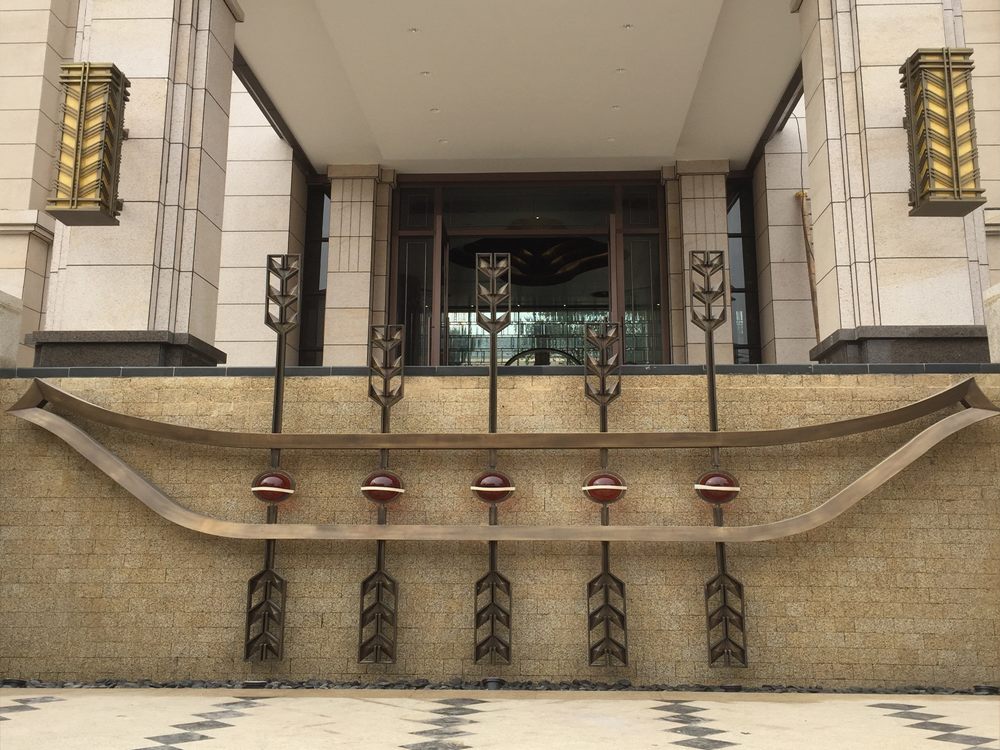
Creating bronze sculptures with hollow interiors is a complex and demanding process that requires meticulous craftsmanship. One of the most significant challenges is ensuring structural integrity. Hollow interiors reduce weight and material costs but can compromise stability if not properly designed. Artists must carefully plan the thickness of the bronze walls to prevent collapse or deformation during the casting process.
Another common issue is achieving uniform wall thickness. Uneven sections can lead to weak spots or cracks, especially during cooling. Skilled sculptors use precise measurements and molds to maintain consistency. Additionally, the casting process itself poses difficulties. Molten bronze must flow evenly into the mold to avoid air pockets or incomplete fills, which can ruin the sculpture.
Ventilation is also critical. Trapped gases during casting can cause bubbles or imperfections. Artists often incorporate vents in their molds to allow gases to escape. Finally, finishing a hollow bronze sculpture requires extra care. Polishing and patinating the interior surfaces can be challenging due to limited access, demanding specialized tools and techniques.
Despite these hurdles, mastering hollow bronze sculptures allows artists to create larger, lighter, and more dynamic works, pushing the boundaries of metal artistry.