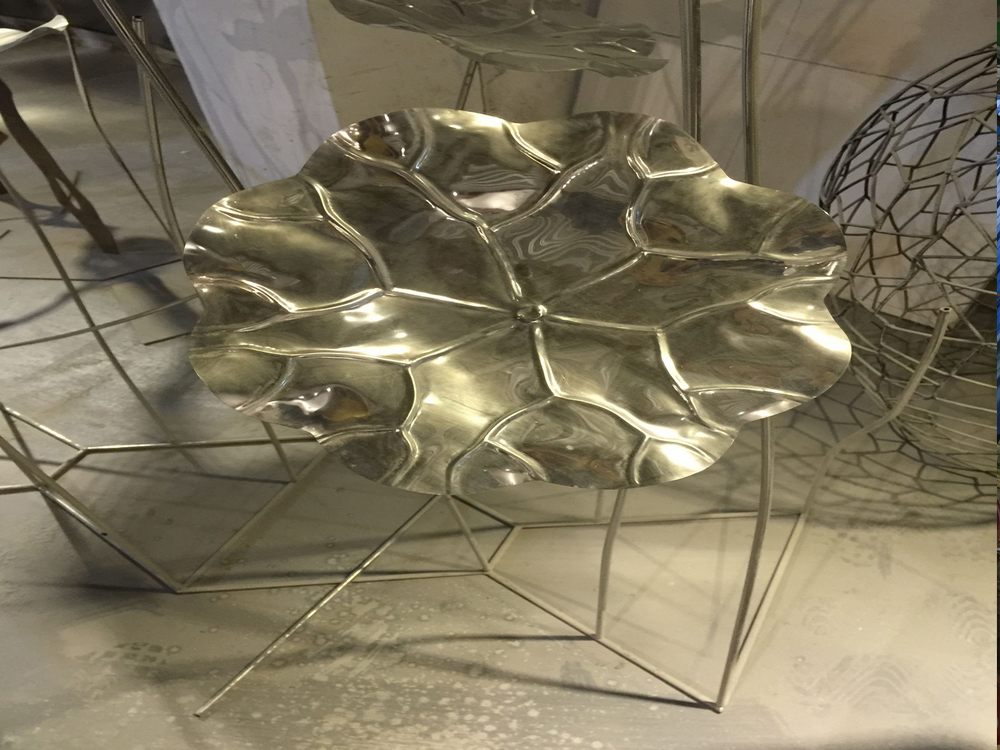
Glaze defects in porcelain sculpture production can significantly impact the final aesthetic and structural quality of the artwork. One of the most frequent causes is improper kiln temperature control. If the kiln is too hot or too cold, the glaze may not fuse correctly, leading to issues like crawling, blistering, or pinholing.
Another common issue stems from material impurities. Contaminants in the clay or glaze mixture, such as dust or foreign particles, can create uneven surfaces or discoloration. Similarly, inadequate mixing or incorrect glaze formulation may result in inconsistent textures or color variations.
Application errors also play a major role. Applying glaze too thickly or too thinly can cause cracking, peeling, or dull finishes. Additionally, insufficient drying time before firing may trap moisture, leading to bubbling or warping.
Finally, rapid cooling or uneven heating in the kiln can introduce thermal shock, causing cracks or glaze separation. By understanding these common pitfalls, artists and manufacturers can take preventive measures to ensure flawless porcelain sculptures.