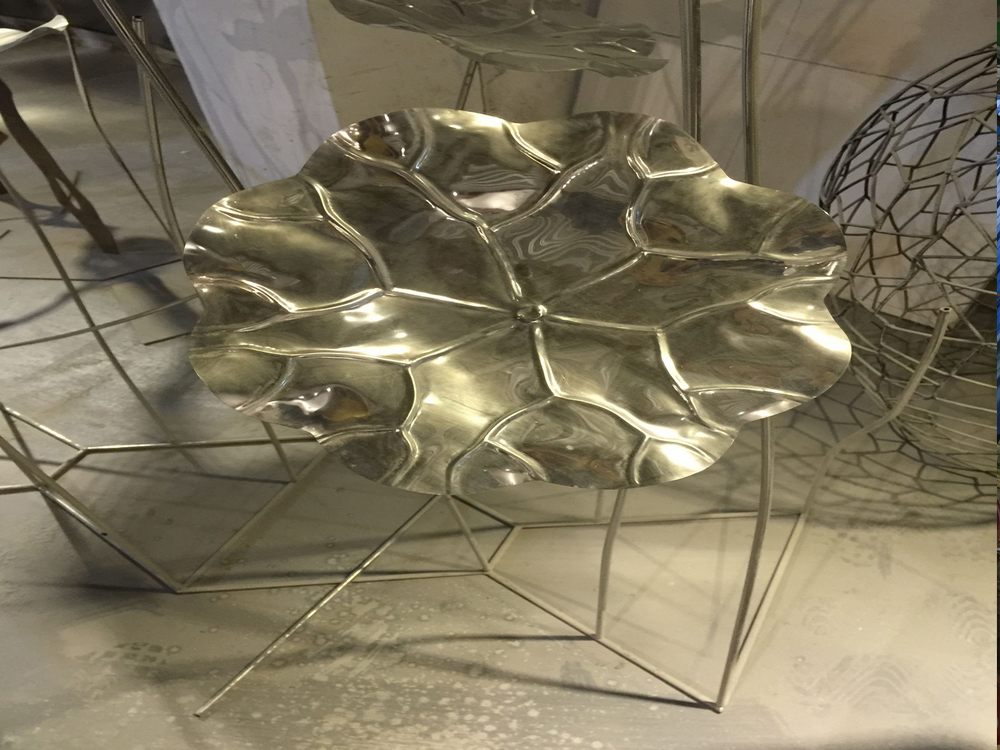
Glaze crazing, the fine network of cracks that appears on the surface of porcelain sculptures, is a common yet frustrating issue for ceramic artists. Understanding its causes can help prevent this defect and preserve the beauty of your work.
1. Thermal Shock: Rapid temperature changes during firing or cooling can cause the glaze and clay body to contract at different rates, leading to stress cracks. Always follow controlled cooling cycles.
2. Glaze-Clay Mismatch: If the glaze’s thermal expansion coefficient doesn’t match the clay body, tension builds as the piece cools, resulting in crazing. Test glazes on small samples before full application.
3. Overfiring or Underfiring: Incorrect kiln temperatures weaken the glaze’s bond with the clay. Overfiring may make the glaze too fluid, while underfiring leaves it brittle and prone to cracking.
4. Thick Glaze Application: Excess glaze layers shrink more than the clay, increasing stress. Apply thin, even coats and avoid pooling in crevices.
5. Aging and Environmental Stress: Humidity and temperature fluctuations over time can worsen existing micro-cracks. Store finished pieces in stable conditions.
To fix minor crazing, consider filling cracks with a compatible clear glaze and refiring. For prevention, prioritize proper glaze formulation, firing schedules, and careful handling. By addressing these factors, you can achieve flawless, durable porcelain sculptures.