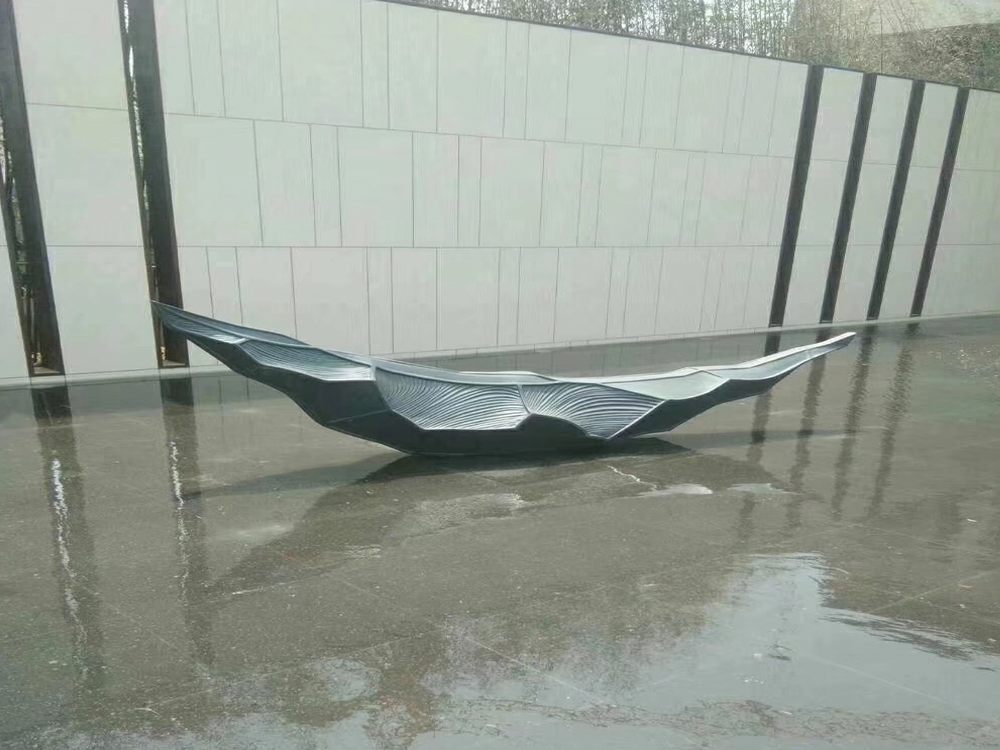
Creating monumental porcelain sculptures is a delicate dance between artistic vision and engineering precision. Artists employ several key strategies to prevent structural failure in these fragile yet ambitious works.
Material innovation forms the foundation of success. Many sculptors blend specially formulated porcelain clays with reinforcing additives like paper fibers or grog (pre-fired clay particles) to improve tensile strength. The clay's plasticity and shrinkage rate are carefully calculated to accommodate the sculpture's scale.
Construction techniques make or break large pieces. Artists often build in sections using coil, slab, or press-mold methods, allowing each component to dry evenly. Strategic internal armatures of kiln-safe materials provide hidden support without compromising the ceramic purity. Some create hollow forms with carefully designed ventilation holes to prevent trapped air explosions during firing.
The kiln process requires masterful control. Multi-stage firing with precisely ramped temperatures allows gradual moisture release. Large works may require custom-built kilns or sectional firing where pieces are assembled after baking. Glazing presents another challenge—artists often apply multiple thin layers to avoid cracking from uneven thermal expansion.
Contemporary artists like Ai Weiwei and Clare Twomey have pushed boundaries by combining traditional ceramic knowledge with modern technology. Digital modeling helps predict stress points, while 3D-printed porcelain components enable unprecedented scale. Ultimately, successful large-scale porcelain art balances centuries-old craft with innovative problem-solving—where every centimeter of expansion and every degree of temperature carries artistic consequence.